Production of 4,4-dimethyl-3-ketone-methoxycarbonyl valerate
A technology of methyl valerate and methyl pivalate, applied in the field of chemical engineering, to achieve the effects of low volatilization loss, easy recovery, and reduced energy consumption
- Summary
- Abstract
- Description
- Claims
- Application Information
AI Technical Summary
Problems solved by technology
Method used
Image
Examples
Embodiment 1
[0028] Weigh 4.6 grams (0.04 moles) of anhydrous methyl pivalate, 1.6 grams of 60% pure sodium hydride (0.04 moles) dispersed in mineral oil and 20 milliliters of dry toluene, mix and stir under nitrogen protection to form a suspension, At the same time, the temperature was raised to 60-65° C., and then a total of 3 g of dry methyl acetate (0.04 mol) was added dropwise. After the addition was completed within about 0.5 hours, the stirring reaction was continued for 1 hour. Cool to room temperature with stirring. Add 4-5 grams of crushed ice to the reaction solution, then add about 7 ml of 5 mol / L hydrochloric acid to pH 4-5, stir and separate layers, remove the lower aqueous phase, and wash twice with 10 ml of clean water until neutral. The organic phase was dehydrated and filtered with anhydrous sodium sulfate, and the toluene was recovered by distillation; after the solvent was removed, the product 1,4-dimethyl-3-keto-methyl valerate was extracted by distillation under reduc...
Embodiment 2
[0030] Under nitrogen protection, 23.2 grams (0.2 moles) of anhydrous methyl pivalate were dissolved in 100 milliliters of dry toluene, and then 8 grams of sodium hydride (0.2 moles) of 60% purity dispersed in mineral oil were added at one time, and stirred The temperature was raised to 65-70°C, and then a total of 14.8 g of dry methyl acetate (0.2 mol) was slowly added dropwise, and the addition was completed within about 1 hour, and the reaction was continued to stir for 1 hour. Cool to room temperature with stirring. Add 20 grams of crushed ice to the reaction liquid, then add about 42 ml of 5 mol / L hydrochloric acid to pH 4-5, stir and separate layers, remove the lower aqueous phase, and wash twice with 50 ml of clean water until neutral. The organic phase was dehydrated and filtered with anhydrous sodium sulfate, and the toluene was recovered by distillation; after the solvent was removed, the product 1,4-dimethyl-3-keto-methyl valerate was extracted by distillation under...
Embodiment 3
[0032] Weigh 80 grams of 60% sodium hydride (2 moles) and add it into a reaction flask with nitrogen gas, then add 1000 milliliters of dry toluene and 232 grams (2 moles) of anhydrous methyl pivalate at one time, and heat up to 60- 65°C, and then slowly add a total of 148 g of dry methyl acetate (2 moles) dropwise, and the addition is completed within about 2 hours, and the reaction is continued for 2 hours with stirring. Cool to room temperature with stirring. Add 200 grams of crushed ice to the reaction liquid, then add about 420 ml of 5mol / L hydrochloric acid to pH 4-5, stir and then separate into layers, remove the lower aqueous phase, and wash twice with 500 ml of clean water until neutral. The organic phase was dehydrated and filtered with anhydrous sodium sulfate, and the toluene was recovered by distillation; after the solvent was removed, the product 1,4-dimethyl-3-keto-methyl valerate was extracted by distillation under reduced pressure to obtain 290 grams of 1 with ...
PUM
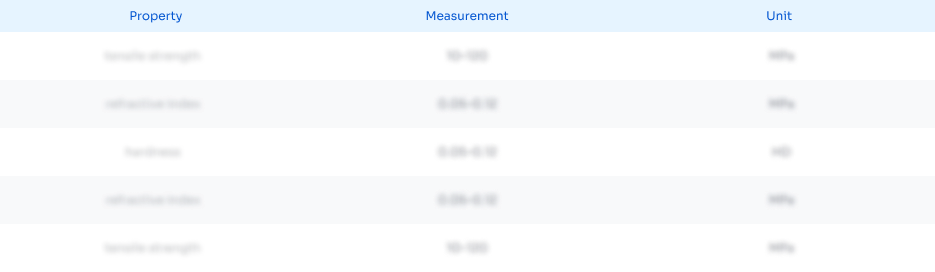
Abstract
Description
Claims
Application Information

- Generate Ideas
- Intellectual Property
- Life Sciences
- Materials
- Tech Scout
- Unparalleled Data Quality
- Higher Quality Content
- 60% Fewer Hallucinations
Browse by: Latest US Patents, China's latest patents, Technical Efficacy Thesaurus, Application Domain, Technology Topic, Popular Technical Reports.
© 2025 PatSnap. All rights reserved.Legal|Privacy policy|Modern Slavery Act Transparency Statement|Sitemap|About US| Contact US: help@patsnap.com