Piezoelectric film cantilever beam type micro-force sensor micro-force loading device
A micro-force sensor and cantilever beam technology, which is applied in the field of static and quasi-static testing and calibration, can solve problems such as micro-newton force loading instability control, and achieve simple and reliable structure, improved calibration accuracy, and convenient operation.
- Summary
- Abstract
- Description
- Claims
- Application Information
AI Technical Summary
Problems solved by technology
Method used
Image
Examples
Embodiment Construction
[0014] The implementation of the present invention will be described in detail below in conjunction with the accompanying drawings. Firstly, the piezoelectric thin film cantilever micro force sensor 27 is processed by bulk silicon processing technology and surface processing technology. Fix the cantilever beam type micro-force sensor 27 on the stage 28, and then place the stage 28 on the shock-absorbing platform 29 to be tested. During measurement and calibration, all devices are integrated and fixed on the shock-absorbing platform 29, and all devices and devices are covered with a windshield.
[0015] This kind of micro force loading device used for the calibration of piezoelectric film cantilever beam type micro force sensor is suitable for working in a clean room with a constant temperature environment of 23°C. First drill a blind hole with a diameter of 1mm at the center of the square fixing block 22, and fix the microprobe 21 in the blind hole with an adhesive; , fixed ...
PUM
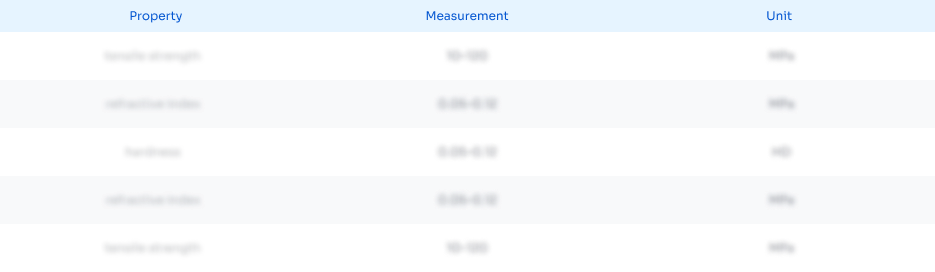
Abstract
Description
Claims
Application Information

- R&D
- Intellectual Property
- Life Sciences
- Materials
- Tech Scout
- Unparalleled Data Quality
- Higher Quality Content
- 60% Fewer Hallucinations
Browse by: Latest US Patents, China's latest patents, Technical Efficacy Thesaurus, Application Domain, Technology Topic, Popular Technical Reports.
© 2025 PatSnap. All rights reserved.Legal|Privacy policy|Modern Slavery Act Transparency Statement|Sitemap|About US| Contact US: help@patsnap.com