Large six-component measurement and angle-variable support device
A technology of support device and six-component force, applied in the direction of measuring device, measuring force component, engine test, etc., can solve the problem of slow response speed and can not achieve quick release, etc., to achieve flexible control method, fast response speed and reliability. locking effect
- Summary
- Abstract
- Description
- Claims
- Application Information
AI Technical Summary
Problems solved by technology
Method used
Image
Examples
Embodiment Construction
[0066] Below in conjunction with accompanying drawing, the present invention is described in detail, specifically as follows:
[0067] Such as figure 1 As shown, a large-scale six-component force measurement and variable angle support device includes a base 100, a six-component force measurement and in-situ calibration device 200, a variable angle device 300 and a locking device 400; a six-component force measurement and in-situ calibration device 200 is installed on the base 100, the variable angle device 300 is installed on the six-component force measurement and in-situ calibration device 200, and the locking device 400 is located on both sides of the variable angle device 300; before the test, the engine is installed on the variable angle device 300, The initial calibration is performed by the six-component force measurement and in-situ calibration device 200. After the calibration is completed, the locking device 400 and the upper platform of the variable angle device 300...
PUM
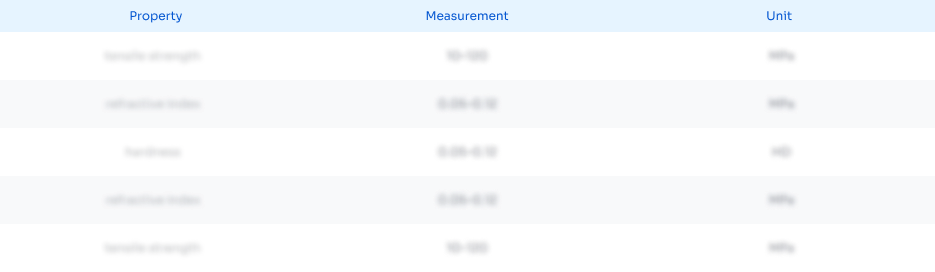
Abstract
Description
Claims
Application Information

- R&D
- Intellectual Property
- Life Sciences
- Materials
- Tech Scout
- Unparalleled Data Quality
- Higher Quality Content
- 60% Fewer Hallucinations
Browse by: Latest US Patents, China's latest patents, Technical Efficacy Thesaurus, Application Domain, Technology Topic, Popular Technical Reports.
© 2025 PatSnap. All rights reserved.Legal|Privacy policy|Modern Slavery Act Transparency Statement|Sitemap|About US| Contact US: help@patsnap.com