Driving belt
A transmission belt and rubber layer technology, applied in the field of transmission belts, can solve the problems of reduced adhesion, difficulty in bonding, heat resistance, wear resistance and insufficient abnormal noise prevention, etc., to achieve abnormal noise prevention and excellent heat resistance sexual effect
- Summary
- Abstract
- Description
- Claims
- Application Information
AI Technical Summary
Problems solved by technology
Method used
Image
Examples
Embodiment 1~12
[0065] (Examples 1-12, Comparative Examples 1-4)
[0066] Manufacture of adhesive and compression rubber layers
[0067] Adhesive rubber layers were prepared from the rubber mixtures shown in Table 1, and after kneading with a Banbury mixer, they were calendered with calender rolls to prepare rubber mixture unvulcanized sheets for the adhesive rubber layers. A compression rubber layer was prepared from the rubber mixture shown in Table 2, and an unvulcanized sheet of the rubber mixture for the compression rubber layer was similarly prepared. In addition, the commercially available items used are as follows.
[0068] Ethylene-propylene-diene rubber (EPDM):
[0069] "X-3012P" (diene content 3.5 mass%, ethylene content 72 mass%, propylene content 24.5 mass%, Mooney viscosity ML 1+4(100°C) is 15, manufactured by Mitsui Chemicals),
[0070] "3085" (diene content of 4.5% by mass, ethylene content of 62% by mass, propylene content of 33.5% by mass, Mooney viscosity ML 1+4 (100°C...
PUM
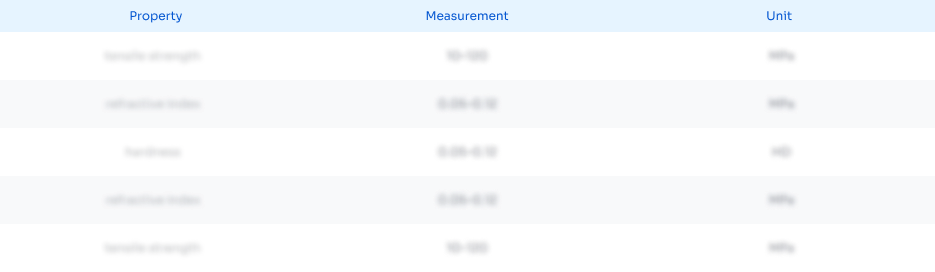
Abstract
Description
Claims
Application Information

- R&D Engineer
- R&D Manager
- IP Professional
- Industry Leading Data Capabilities
- Powerful AI technology
- Patent DNA Extraction
Browse by: Latest US Patents, China's latest patents, Technical Efficacy Thesaurus, Application Domain, Technology Topic, Popular Technical Reports.
© 2024 PatSnap. All rights reserved.Legal|Privacy policy|Modern Slavery Act Transparency Statement|Sitemap|About US| Contact US: help@patsnap.com