Friction transmission belt and process for producing the same
A technique for friction transmission belts and manufacturing methods, applied in transmission belts, waist belts, V-shaped belts, etc., can solve problems such as insufficient adhesion, decreased adhesion, and difficult adhesion, so as to improve adhesion and prevent core wires The effects of collapse and excellent dynamic life
- Summary
- Abstract
- Description
- Claims
- Application Information
AI Technical Summary
Problems solved by technology
Method used
Image
Examples
Embodiment 1~4 and comparative example 1~7
[0129] (handling of core wire)
[0130] Polyethylene terephthalate core wire (PET thread, 1000 denier (denier), / 2×3, final twist (upper burning り) is 9.5T / 10cm (Z), initial twist (lower burning ri) 21.9T / 10cm, manufactured by Teijin Corporation) was immersed in a toluene solution of isocyanate (solid content of isocyanate: 20% by mass), and then heat-dried at 240° C. for 40 seconds to perform pretreatment.
[0131] Next, the thus-pretreated polyethylene terephthalate cord was dipped in the obtained RFL adhesive composition, and heated and dried at 230° C. for 80 seconds to perform an adhesive treatment.
[0132] Then, after dipping the thus-treated polyethylene terephthalate cord into the rubber paste, it was heated and dried at 60° C. for 40 seconds, and the polyethylene terephthalate cord was bonded ( post-processing).
[0133] (Manufacture of friction transmission belt)
[0134] The canvas and the above-mentioned unvulcanized sheet of rubber mixture used for bonding the...
Embodiment 5~6
[0136] Instead of polyethylene terephthalate core wire, use polyethylene naphthalate core wire (PEN wire, 1000 denier, / 2×3, final twist 9.5T / 10cm(Z), initial Twist 21.9T / 10cm, manufactured by Teijin Corporation, Example 5), aramid core wire (aramid thread, 1000 denier, / 2×3, final twist 9.5T / 10cm(Z), The initial twist is 21.9T / 10cm, manufactured by Teijin Corporation, Example 6), except that, in the same manner as in Example 1, the processing of the core wire and the production of the friction transmission belt were carried out.
[0137] [evaluate]
[0138] Adhesion test and conveyor belt running test were carried out by the following methods, and the peel adhesion and failure mode in the adhesion test and the peeling length after belt running in the conveyor belt running test were evaluated. The results are shown in Table 5.
PUM
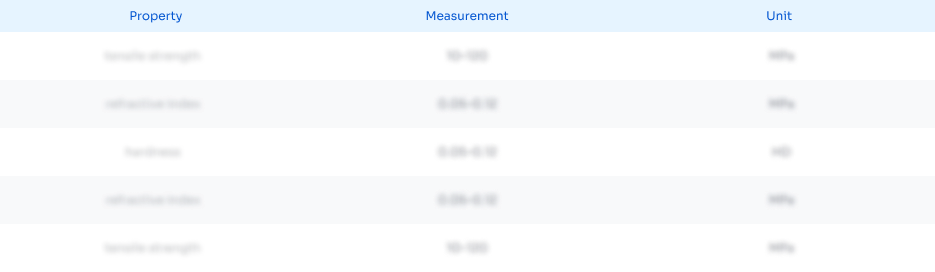
Abstract
Description
Claims
Application Information

- R&D Engineer
- R&D Manager
- IP Professional
- Industry Leading Data Capabilities
- Powerful AI technology
- Patent DNA Extraction
Browse by: Latest US Patents, China's latest patents, Technical Efficacy Thesaurus, Application Domain, Technology Topic, Popular Technical Reports.
© 2024 PatSnap. All rights reserved.Legal|Privacy policy|Modern Slavery Act Transparency Statement|Sitemap|About US| Contact US: help@patsnap.com