Method for preparing acrylic acid esters co-polymer membrane with anticoagulation function
A technology of acrylate and copolymer membranes, applied in chemical instruments and methods, membrane technology, semi-permeable membrane separation, etc., can solve problems such as not resistant to high temperature disinfection, poor mechanical strength, etc.
- Summary
- Abstract
- Description
- Claims
- Application Information
AI Technical Summary
Problems solved by technology
Method used
Image
Examples
Embodiment 1
[0027] Add azobisisobutyronitrile, chloroform and N,N-dimethylformamide in turn to the container at room temperature, stir to make them fully mixed, transfer them into the polymerization reactor, and then add acryloyloxyethyl methyl ester and methyl acrylate, so that the molar ratio of methyl acrylate: acryloyloxyethyl methyl ester: azobisisobutyronitrile is 1: 0.50: 0.02, and the amount of total solvent is 8 times of the total monomer mass , The consumption of N,N-dimethylformamide is 50% of the total solvent mass. Continuously feed high-purity nitrogen for 10-40 minutes to remove oxygen, seal it, then place the polymerization reactor in a constant temperature water bath at 50°C, and oscillate (oscillation frequency 100-300rpm) for 24 hours. After the reaction was complete, the copolymer was precipitated with ether, filtered, and dried in vacuo.
[0028] Weigh a certain mass of copolymer in a container, use chloroform and N,N-dimethylformamide as solvents, adjust the concent...
Embodiment 2
[0030] Add dibenzoyl peroxide, chloroform and N,N-dimethylformamide in sequence at room temperature, stir to make them fully mixed, transfer them into the polymerization reactor, and then add acryloyl nonaoxyethyl formamide base ester and methyl methacrylate, so that methyl methacrylate: acryloyl nonaoxyethyl methyl ester: the material ratio of dibenzoyl peroxide is 1: 0.40: 0.015, and the consumption of total solvent is the total 9 times the mass of the monomer, and the amount of N,N-dimethylformamide is 40% of the total solvent mass. Continuously feed high-purity nitrogen for 10-40 minutes to remove oxygen, seal it, then heat the polymerization reactor to 60°C, stir (stirring frequency 100-300rpm) and react for 18 hours. After the reaction was complete, the copolymer was precipitated with ether, filtered, and dried in vacuo.
[0031] Weigh a certain mass of copolymer in a container, use chloroform and N,N-dimethylformamide as solvents, adjust the concentration of the copoly...
Embodiment 3
[0033]Add azobisisobutyronitrile, chloroform and ethanol in sequence in the container at room temperature, stir to make them fully mixed, transfer them to the polymerization reactor, and then add 2-methacryloyl dioxyethyl methyl ester and acrylic acid Methyl acrylate, so that methyl acrylate: 2-methacryloyl dioxyethyl methyl ester: azobisisobutyronitrile ratio of substances is 1: 0.30: 0.01, the amount of total solvent is the total monomer mass 10 times, the consumption of ethanol is 30% of total solvent mass. Continuously feed high-purity nitrogen for 10-40 minutes to remove oxygen, seal it tightly, then place the polymerization reactor in a constant temperature water bath at 70°C, and oscillate (oscillation frequency 100-300rpm) for 12 hours. After the reaction was complete, the copolymer was precipitated with ether, filtered, and dried in vacuo.
[0034] Weigh a certain mass of copolymer into a container, use chloroform and ethanol as solvents, adjust the concentration of ...
PUM
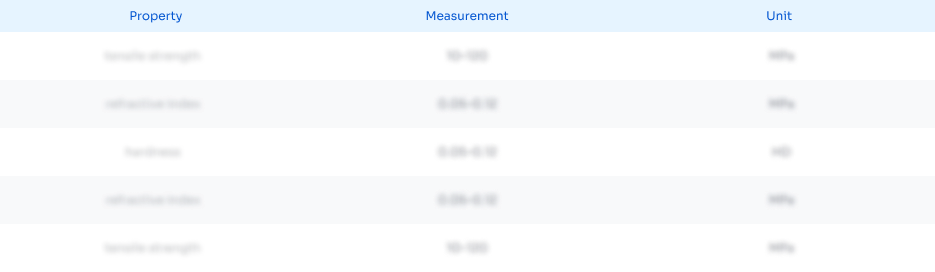
Abstract
Description
Claims
Application Information

- R&D Engineer
- R&D Manager
- IP Professional
- Industry Leading Data Capabilities
- Powerful AI technology
- Patent DNA Extraction
Browse by: Latest US Patents, China's latest patents, Technical Efficacy Thesaurus, Application Domain, Technology Topic, Popular Technical Reports.
© 2024 PatSnap. All rights reserved.Legal|Privacy policy|Modern Slavery Act Transparency Statement|Sitemap|About US| Contact US: help@patsnap.com