Exhaust system and method for joining components of an exhaust system
A technology of exhaust system and connection method, which is applied to exhaust devices, welding equipment, engine components, etc., and can solve problems such as unfavorable strength and impact
- Summary
- Abstract
- Description
- Claims
- Application Information
AI Technical Summary
Problems solved by technology
Method used
Image
Examples
Embodiment Construction
[0025] FIG. 1 shows two components 10 and 12 , in the present embodiment two ducts for an exhaust system of a motor vehicle. Here, it should be noted that basically components other than pipes can also be connected to each other, such as a funnel with a pipe, a funnel with a casing, and the like.
[0026] The first part 10 has a constant cross-section, while the end of the second part 12 facing the first part 10 has an outwardly facing bead 14 and an insertion portion 16 close to the bead 14 . The outer diameter of the insert part 16 is slightly smaller than the inner diameter of the first part 10 .
[0027] The region of the weld bead 14 facing the component 10 and arranged perpendicular to the middle axis M forms a support surface 18 on which the annular solder 20 rests. In this way, the solder is located in the region of the solder joint formed between the insert part 16 of the second component 12 and the first component 10 . The solder 20 is a copper-based or nickel-base...
PUM
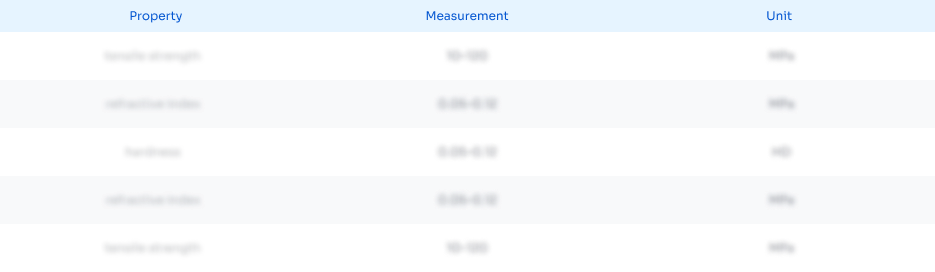
Abstract
Description
Claims
Application Information

- R&D
- Intellectual Property
- Life Sciences
- Materials
- Tech Scout
- Unparalleled Data Quality
- Higher Quality Content
- 60% Fewer Hallucinations
Browse by: Latest US Patents, China's latest patents, Technical Efficacy Thesaurus, Application Domain, Technology Topic, Popular Technical Reports.
© 2025 PatSnap. All rights reserved.Legal|Privacy policy|Modern Slavery Act Transparency Statement|Sitemap|About US| Contact US: help@patsnap.com