Production of medium-high voltage anode corrosive foil
A manufacturing method and anode foil technology, applied in capacitor electrodes, capacitor parts and other directions, can solve the problems of high manufacturing cost and environmental protection cost, unfavorable promotion, low output, etc., and achieve low production cost and environmental protection cost and good overall stability. , controllable effect
- Summary
- Abstract
- Description
- Claims
- Application Information
AI Technical Summary
Problems solved by technology
Method used
Examples
Embodiment 1
[0045] Corrosion foil implementation scheme in the medium-pressure section: imported Showa CH99 model 110um thick light foil, at about 5wt%H3 PO 4 In the bath, the temperature is 50°C, and the treatment is 45Sec: After washing with water, it is charged with direct current in an electrolysis, and the current density is 0.25A / cm 2 , the temperature is 89°C, the treatment is 3×45Sec (a 3V electrolytic cell), and the electrolytic cell solution is composed of 25Wt% H 2 SO 4 +3.5Wt% HCL+1Wt% aluminum ion composition; after washing, treat in 4Wt% ammonia water for 45Sec, the temperature is 75°C; after washing, in 4Wt% NH 4 At 0.10A / cm in Cl secondary electrolyte 2 DC power plus electrolysis 2×(4×45)Sec (two electrolyzers, each tank 4V), the temperature is 90°C; after washing with water, in 3Wt%HNO 3 Medium treatment 45Sec, the temperature is 60 ° C; after washing with 8Wt% HNO 3 +0.1Wt% corrosion inhibitor in the three electrolytes at 0.15A / cm 2 DC power plus electrolysis (4×45+...
Embodiment 2
[0048] Implementation of corrosion foil in the high-pressure section: HEC 115um thickness light foil is used, and the cubic texture requirement is greater than 97%; after being treated with 2Wt% NaOH alkaline pretreatment solution at a temperature of 38°C for 50Sec, it is washed with water and continued to be washed with 3Wt% h 3 PO 4 Acidic treatment solution, at a temperature of 50°C, for 50Sec; after washing with water, apply DC power in an electrolysis with a current density of 0.30A / cm 2 , the temperature is 82°C, the treatment is 2×50Sec (a 2V electrolyzer), and the electrolyzer liquid is composed of 30Wt% H 2 SO 4 +3Wt% HCL+1Wt% aluminum ion composition; after washing, treat in 4Wt% ammonia water for 50Sec, the temperature is 75°C; after washing, in 4Wt% NH 4 At 0.10A / cm in Cl secondary electrolyte 2 DC power plus electrolysis (4×50+2×50) Sec (two electrolytic tanks, one tank 4V, one tank 2V), the temperature is 88 ° C: after washing in 3Wt% HNO 3 Medium treatment ...
PUM
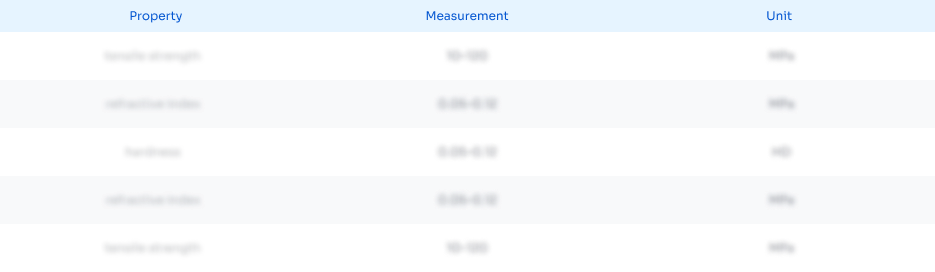
Abstract
Description
Claims
Application Information

- R&D
- Intellectual Property
- Life Sciences
- Materials
- Tech Scout
- Unparalleled Data Quality
- Higher Quality Content
- 60% Fewer Hallucinations
Browse by: Latest US Patents, China's latest patents, Technical Efficacy Thesaurus, Application Domain, Technology Topic, Popular Technical Reports.
© 2025 PatSnap. All rights reserved.Legal|Privacy policy|Modern Slavery Act Transparency Statement|Sitemap|About US| Contact US: help@patsnap.com