High-speed electrospraying device
A high-speed, bath technology, applied in the field of mechanical devices, can solve the problems of difficult to obtain composite coating, unsatisfactory and unsatisfactory particle content of the coating, and achieve the effects of novel structure, reduced thickness and accelerated stirring speed.
- Summary
- Abstract
- Description
- Claims
- Application Information
AI Technical Summary
Problems solved by technology
Method used
Image
Examples
Embodiment
[0016] In the high-speed electrospraying device, since the magnetic pump is forbidden to work under the condition of lack of liquid, the magnetic pump is designed at the bottom of the console. The sunken design is the deposition chamber, and all the connecting parts in the device are riveted with stainless steel. When working, the magnetic pump runs to make the plating solution circulate at a high speed in the liquid storage tank, the plating solution tank and the stainless steel pipeline, and the flow meter installed in the stainless steel pipeline controls the flow of the plating solution, and is filtered by the installed filter valve The impurities in it realize the high-speed injection and recycling of the plating solution. And through the installed regulating valve, it is guaranteed to flow into the liquid storage tank at the lowest point of the entire circulation device, to ensure the effectiveness of the plating solution, and to facilitate the storage of the plating sol...
PUM
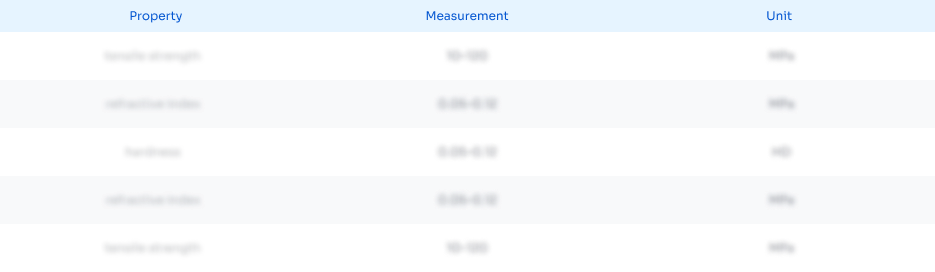
Abstract
Description
Claims
Application Information

- R&D Engineer
- R&D Manager
- IP Professional
- Industry Leading Data Capabilities
- Powerful AI technology
- Patent DNA Extraction
Browse by: Latest US Patents, China's latest patents, Technical Efficacy Thesaurus, Application Domain, Technology Topic, Popular Technical Reports.
© 2024 PatSnap. All rights reserved.Legal|Privacy policy|Modern Slavery Act Transparency Statement|Sitemap|About US| Contact US: help@patsnap.com