How to Improve The Thermal Stability Of PVDF (Polyvinylidene Fluoride)?
Technology Background And Goals
In this technical report, you will learn how to improve the thermal stability of PVDF (polyvinylidene fluoride), a widely used polymer with excellent chemical resistance, mechanical strength, and electrical properties. PVDF's thermal stability is a crucial factor determining its performance and application scope in various industries, such as energy storage, electronics, and membranes.
Enhancing PVDF's thermal stability can expand its potential applications in high-temperature environments, enabling its use in advanced technologies like lithium-ion batteries, fuel cells, and high-performance electronics. Improving thermal stability can also prolong the material's service life and reduce maintenance costs in existing applications.
PVDF Market Demand Analysis
- Market Size and Growth
PVDF has a substantial and growing market, driven by its applications in lithium-ion batteries, membranes, and coatings. The global PVDF market is projected to reach $1.2 billion by 2027, with a CAGR of 6.2% from 2022 to 2027. - Key Application Areas
- Lithium-ion batteries: PVDF is widely used as a binder in electrodes, contributing to the growing demand from the electric vehicle and renewable energy sectors.
- Membranes: PVDF membranes are used in water treatment, biopharmaceuticals, and chemical processing due to their chemical resistance and thermal stability.
- Coatings: PVDF coatings are valued for their durability, weather resistance, and corrosion protection in construction and automotive industries.
- Regional Market Dynamics
Asia Pacific dominates the PVDF market, driven by the rapid growth of end-use industries in countries like China, India, and South Korea. North America and Europe also have significant demand, particularly in the automotive and construction sectors. - Emerging Trends
- Increasing demand for sustainable and energy-efficient solutions is driving the adoption of PVDF in renewable energy and water treatment applications.
- The growing electric vehicle market is expected to boost the demand for PVDF as a binder material in lithium-ion batteries.
- The development of new PVDF grades with improved thermal stability and mechanical properties could open up new application areas.
Technology Status And Challenges
- Thermal Stability Challenges PVDF exhibits poor thermal stability, undergoing dehydrofluorination and chain scission reactions at elevated temperatures, leading to material degradation and performance loss.
- Geographical Distribution Research on PVDF thermal stability is globally distributed, with major contributions from the United States, Europe, China, Japan, and South Korea.
- Key Technical Hurdles
- Understanding the complex degradation mechanisms at the molecular level
- Developing effective stabilization strategies to inhibit degradation reactions
- Enhancing thermal resistance while maintaining desirable properties
Technology Evolution Path
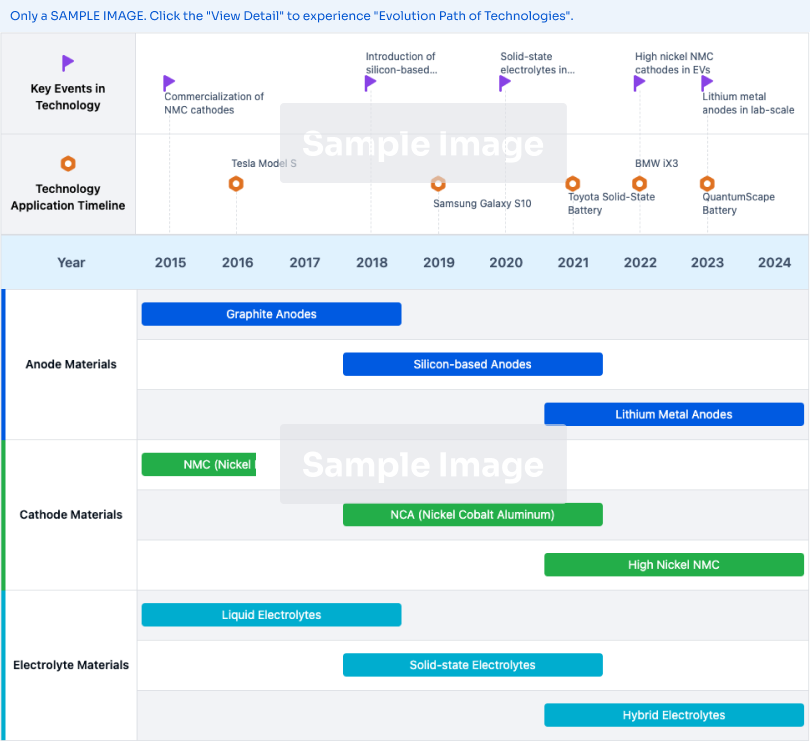
Current Technical Solutions
01 Copolymerization
Copolymerizing PVDF with monomers like hexafluoropropylene (HFP) or chlorotrifluoroethylene (CTFE) can introduce structural modifications that enhance its thermal stability.- Copolymerization: Copolymerizing PVDF with monomers like hexafluoropropylene (HFP) or chlorotrifluoroethylene (CTFE) can introduce structural modifications that enhance its thermal stability.
- Nanocomposite Formation: Forming nanocomposites by adding nanofillers like carbon nanotubes, graphene, or metal oxides to PVDF can improve its thermal resistance and decomposition temperature.
- Crosslinking: Crosslinking PVDF chains through radiation or chemical methods can increase resistance to chain scission and decomposition at high temperatures, thereby enhancing thermal stability.
- Polymer Blending: Blending PVDF with thermally stable polymers like polyimides, polysulfones, or polyetheretherketones (PEEK) can increase the overall thermal resistance of the blend.
- Additives and Fillers: Incorporating additives and fillers like thermal stabilizers, antioxidants, or heat-resistant fillers into PVDF can improve its thermal stability.
02 Nanocomposites
Incorporating nanofillers or nanoparticles into PVDF to form nanocomposites can improve its thermal resistance, as the nanofillers act as thermal barriers or heat dissipaters.03 Crosslinking
Crosslinking PVDF chains through radiation or chemical crosslinking agents can increase molecular weight and reduce chain mobility, thereby improving thermal stability.04 Blending
Blending PVDF with other thermally stable polymers or additives can improve its overall thermal stability, as the blending components can act as thermal stabilizers or provide synergistic effects.05 Surface Modification
Surface modification techniques like plasma treatment or chemical grafting can introduce functional groups or coatings that enhance the thermal resistance of PVDF's surface.
Main Player Analysis
Arkema, Inc.
Wanhua Chemical Group Co., Ltd.
Key Technology Interpretation
- The process uses sodium acetate and potassium alkylsulphonate to improve the thermal stability of PVDF.
- The resulting PVDF contains less than 300 ppm of surface-active additive, reducing the impact of surfactant residues on heat stability.
- The process can be carried out in a batchwise or semi-continuous manner, allowing for flexibility in production.
PVDF Thermal Stability Improvement Economic Analysis
Improving the thermal stability of PVDF (Polyvinylidene Fluoride) has significant economic implications, particularly across industries such as electronics, automotive, and renewable energy, where PVDF is extensively used for its advantageous properties like chemical resistance and durability. Enhancing its thermal stability can lead to extended product lifespans, which in turn reduces costs associated with frequent replacements and maintenance, thereby offering economic gains.
By elevating PVDF's thermal thresholds, manufacturers can expand their market offerings, tapping into applications that require higher thermal endurance, such as in high-temperature electronic components, advanced battery systems, and extreme environments. This advancement could lead to increased market share and competitive advantage in sectors looking for materials that provide both performance and reliability under thermal stress.
Furthermore, progress in this area can stimulate innovation in processing techniques and lead to cost reductions in production. As a result, the overall manufacturing efficiency could be improved, decreasing the cost per unit and potentially leading to reductions in pricing for end consumers while maintaining or increasing profit margins.
Implementing strategies that enhance thermal stability could also foster sustainable practices by minimizing waste and resource consumption, which aligns with global trends towards environmental responsibility. Therefore, addressing this technical challenge holds the potential not only for significant economic benefits but also for reinforcing sustainable industrial practices.
PVDF Thermal Stability Improvement Policy And Regulatory Impact
The policy and regulatory landscape plays a crucial role in determining the development and application of technologies aimed at improving the thermal stability of PVDF (Polyvinylidene Fluoride). Regulatory standards related to the safety, performance, and environmental impact of materials often guide the direction of research and innovation. For instance, regulations governing fire safety and smoke generation in various applications can drive the need for PVDF with enhanced thermal properties. Compliance with international standards such as those set by ASTM or ISO ensures that developed technologies are viable for global markets, influencing R&D investments.
Furthermore, environmental regulations pushing for sustainable materials provide incentives for developing PVDF modifications that enhance thermal stability without compromising environmental integrity. Government grants and subsidies may also support research in advanced materials, encouraging companies to develop proprietary technologies to improve PVDF.
In addition, intellectual property rights within regulatory frameworks can impact competitive positioning, as securing unique technological advancements through patents can offer significant market advantages. Understanding these regulatory impacts is essential for aligning technological development with market entry strategies, ensuring that advancements in PVDF meet both current and future regulatory requirements for broader adoption and commercial success.