Polishing method and polishing apparatus
a technology of polishing apparatus and surface, which is applied in the direction of grinding machine components, manufacturing tools, lapping machines, etc., can solve the problems of insufficient polishing rate of surface (to be polished) of substrate, unpolished copper film may remain in scattered state, and the surface to be polished is not easy to achieve sufficient polishing rate. , to achieve the effect of sufficient polishing ra
- Summary
- Abstract
- Description
- Claims
- Application Information
AI Technical Summary
Benefits of technology
Problems solved by technology
Method used
Image
Examples
case 1
[Case 1]
[0054]A substrate W is prepared which, as shown in FIG. 8, has insulating films 902, 903 having via holes 904 and trenches 905, a barrier film 906 formed on the insulating films 902, 903, and a metal film 907 formed on the barrier film 906. Those portions of the metal film 907, which are embedded in the via holes 904 and the trenches 905, constitute metal interconnects. In the case 1, the metal film is a copper film and the metal interconnects are copper interconnects.
[0055]First, the supply pressure of compressed air to be supplied to the cooling nozzles 24 is confirmed. If this supply pressure is less than a specified pressure, a warning is issued and processing of subsequent substrates is stopped. When this supply pressure is not less than a specified pressure, the polishing head 16 in the substrate transfer position receives a substrate W, e.g., from a pusher and holds the substrate W by attraction. The substrate W held by the polishing head 16 is then moved horizontally...
case 2
[Case 2]
[0071]A substrate W as shown in FIG. 8, which is similar to the substrate W of the above-described case 1, is prepared. In the case 2, the metal film 907 is a tungsten film and the metal interconnects are tungsten interconnects.
[0072]First, as with the above-described case 1, the supply pressure of compressed air, to be supplied to the cooling nozzles 24, is confirmed. When this supply pressure is not less than a specified pressure, the polishing head 16 in the substrate transfer position receives a substrate W, e.g., from a pusher and holds the substrate W by attraction. The substrate W held by the polishing head 16 is then moved horizontally from the substrate transfer position to the polishing position just above the polishing table 12.
[0073]Next, monitoring of the temperature of the polishing pad 14 with the thermometer 32 is started. As with the case 1, blowing of compressed air from the cooling nozzles 24 toward the polishing pad 14 is not yet started.
[0074]While suppl...
case 3
[Case 3]
[0079]The case 3 is applicable to an STI (shallow trench isolation) process, a polysilicon removal process, a barrier layer removal process, etc. In the case of an STI process, for example, a substrate W, as shown in FIG. 9, is prepared. The substrate W comprises a silicon wafer 100 having trenches, a pad oxide film 104 which covers the surface of the silicon wafer 100, an SiN film 103 formed on the pad oxide film 104 and lying outside the trenches, and an SiO2 film 102 of a insulating film which fills the trenches of the silicon wafer 100 and covers an entire surface of the substrate W.
[0080]First, as with the above-described case 1, the supply pressure of compressed air, to be supplied to the cooling nozzle 24, is confirmed. When this supply pressure is not less than a specified pressure, the polishing head 16 in the substrate transfer position receives a substrate W, e.g., from a pusher and holds the substrate W by attraction. The substrate W held by the polishing head 16...
PUM
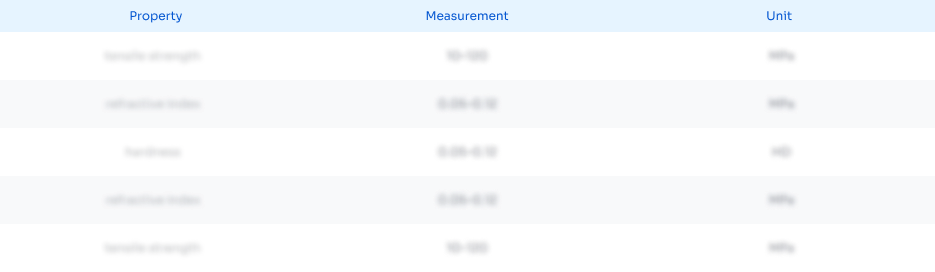
Abstract
Description
Claims
Application Information

- Generate Ideas
- Intellectual Property
- Life Sciences
- Materials
- Tech Scout
- Unparalleled Data Quality
- Higher Quality Content
- 60% Fewer Hallucinations
Browse by: Latest US Patents, China's latest patents, Technical Efficacy Thesaurus, Application Domain, Technology Topic, Popular Technical Reports.
© 2025 PatSnap. All rights reserved.Legal|Privacy policy|Modern Slavery Act Transparency Statement|Sitemap|About US| Contact US: help@patsnap.com