High temperature hydropyrolysis of carbonaceous materials
a carbonaceous material, high temperature technology, applied in the direction of hydrocarbon oil cracking, physical/chemical process catalysts, chemistry apparatuses and processes, etc., to achieve the effect of significant carbon emission reduction and effectively utilized
- Summary
- Abstract
- Description
- Claims
- Application Information
AI Technical Summary
Benefits of technology
Problems solved by technology
Method used
Image
Examples
Embodiment Construction
[0015]In FIG. 1, an illustrative hydropyrolysis unit with heat supplied from nuclear reactor as an external thermal source is shown. A nuclear reactor 10 providing thermal energy is used to provide heat by way of a heat transfer medium in line 11 to a steam generator 12 which feeds an electrical generator 13 with steam via line 14. Units A, B C and D are hydrogen generators of different types, of which one will be selected for the unit, all being shown here to show the different utility connections required for each type of generator. Unit A is either a zinc-zinc oxide cycle generator or a sulfur-iodine cycle generator, electricity as required by way of line 16 and heat service through line 17 with a suitable heat transfer medium in line 17 bringing heat from heat transfer line 11. Unit B is a high temperature steam electrolysis unit which is supplied with both electricity and steam by way of service lines 16 and 17 respectively. Steam may be taken from steam generator 12 by way of ...
PUM
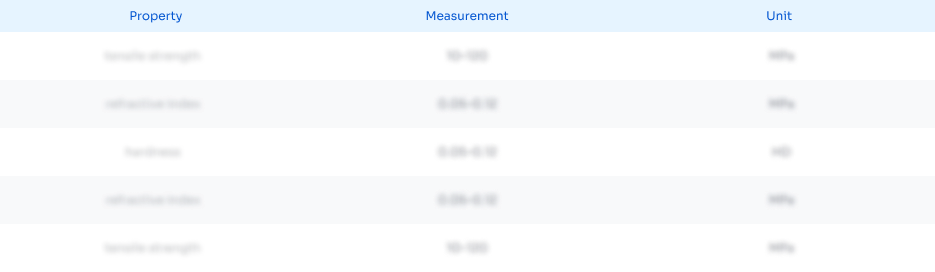
Abstract
Description
Claims
Application Information

- R&D
- Intellectual Property
- Life Sciences
- Materials
- Tech Scout
- Unparalleled Data Quality
- Higher Quality Content
- 60% Fewer Hallucinations
Browse by: Latest US Patents, China's latest patents, Technical Efficacy Thesaurus, Application Domain, Technology Topic, Popular Technical Reports.
© 2025 PatSnap. All rights reserved.Legal|Privacy policy|Modern Slavery Act Transparency Statement|Sitemap|About US| Contact US: help@patsnap.com