Reverse nozzle drill bit
- Summary
- Abstract
- Description
- Claims
- Application Information
AI Technical Summary
Benefits of technology
Problems solved by technology
Method used
Image
Examples
Embodiment Construction
[0048]This disclosure describes a drill bit design that employs a means for promoting efficient and increased upward flow of drilling sludge away from the drilling area and specifically away from the drill bit cutters. The reverse nozzle drill bit employs a singular or a plurality of upward pointing nozzles through which a portion of the pressurized drilling fluid is directed. The resulting flow through the reverse nozzle or reverse nozzles creates a region of relatively lower pressure area between the reverse nozzle or reverse nozzles and the drill bit cutting face. The result of this relatively lower pressure zone is increased flow upward and away from the drill bit cutting face. Additionally, the reverse nozzle or nozzles, which may be directed in a multitude of compound angles and geometric configurations, may additionally create an upward circular flow of drilling sludge.
[0049]FIGS. 1 through 8 describe the reverse nozzle drill bit in a polycrystalline diamond compact (PDC) typ...
PUM
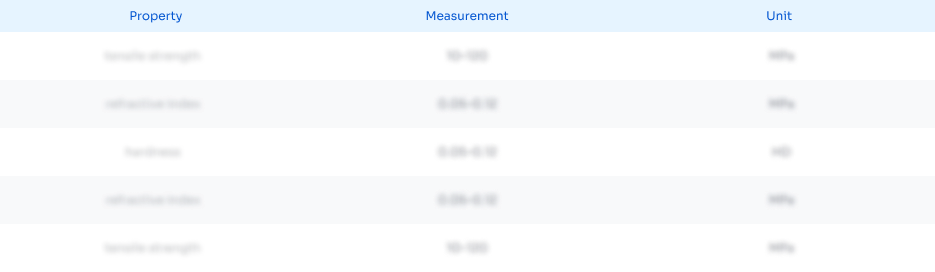
Abstract
Description
Claims
Application Information

- R&D
- Intellectual Property
- Life Sciences
- Materials
- Tech Scout
- Unparalleled Data Quality
- Higher Quality Content
- 60% Fewer Hallucinations
Browse by: Latest US Patents, China's latest patents, Technical Efficacy Thesaurus, Application Domain, Technology Topic, Popular Technical Reports.
© 2025 PatSnap. All rights reserved.Legal|Privacy policy|Modern Slavery Act Transparency Statement|Sitemap|About US| Contact US: help@patsnap.com