Fluid bearing device
a technology of bearings and bearing sleeves, which is applied in the direction of bearings, shafts and bearings, rotary bearings, etc., can solve the problems of high moment rigidity, difficult to accurately perform positioning fixation of this kind, and difficult to manage the clearance of thrust bearings with high accuracy. , the effect of high accuracy
- Summary
- Abstract
- Description
- Claims
- Application Information
AI Technical Summary
Benefits of technology
Problems solved by technology
Method used
Image
Examples
first embodiment
[0033]First, a description is made of the present invention with reference to FIGS. 1 to 5.
[0034]FIG. 1 conceptually illustrates a structural example of a spindle motor for information equipment according to a first embodiment of the present invention, in which a fluid bearing device (dynamic pressure bearing device) 1 is incorporated. The spindle motor is used for a disk drive device such as an HDD. The spindle motor includes a fluid bearing device 1 for rotatably supporting a shaft member 2, a hub 3 fixed to the shaft member 2, a stator coil 4 and a rotor magnet 5 opposed to each other through intermediation of a radial gap, for example, and a bracket 6. The stator coil 4 is mounted to an outer periphery of the bracket 6. The rotor magnet 5 is mounted to an inner periphery of the hub 3. The fluid bearing device 1 is fixed to an inner periphery of the bracket 6. The hub 3 holds one or a plurality of (two in FIG. 1) disks D serving as information recording media. In the spindle moto...
third embodiment
[0085]FIG. 7 is a diagram conceptually illustrating a construction example of an information apparatus spindle motor into which a fluid bearing device (fluid dynamic pressure bearing device) 31 according to the present invention is incorporated. The spindle motor is used in a disk drive, such as an HDD, and is equipped with: the fluid bearing device 31 for rotatably supporting a shaft member 32 in a non-contact manner; a rotor (disk hub) 33 mounted to the shaft member 32; and a stator coil 34 and a rotor magnet 35 opposed to each other through the intermediation of, for example, a radial gap. The stator coil 34 is mounted to an outer periphery of a bracket 36, and the rotor magnet 35 is mounted to an inner periphery of the disk hub 33. A housing 37 of the fluid bearing device 31 is mounted to the inner periphery of the bracket 36. One or a plurality of disks D such as magnetic disks are retained by the disk hub 33. When electricity is supplied to the stator coil 34, the rotor magnet...
second embodiment
[0125]FIG. 6 is a sectional view illustrating a fluid bearing device according to the present invention.
[0126]FIG. 7 is a sectional view illustrating a spindle motor in which a fluid bearing device according to a third embodiment of the present invention is incorporated.
[0127]FIG. 8 is a sectional view of the fluid bearing device according to the third embodiment of the present invention.
[0128]FIG. 9(a) is a view illustrating an upper end surface of a first bearing sleeve, FIG. 9(b) is a longitudinal sectional view of a bearing sleeve, and FIG. 9(c) is a view illustrating a lower end surface of a second bearing sleeve.
[0129]FIG. 10 is a longitudinal sectional view illustrating a bearing sleeve according to another mode of the present invention.
PUM
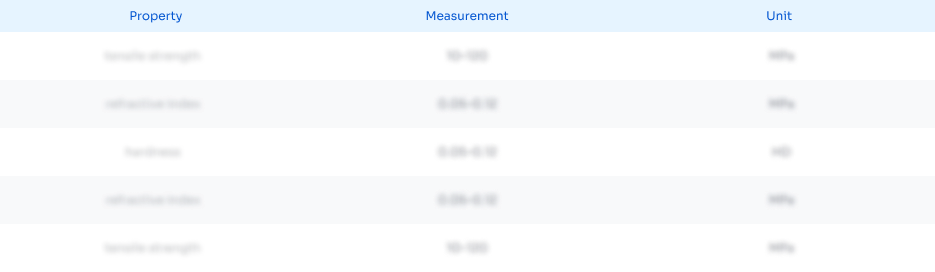
Abstract
Description
Claims
Application Information

- R&D
- Intellectual Property
- Life Sciences
- Materials
- Tech Scout
- Unparalleled Data Quality
- Higher Quality Content
- 60% Fewer Hallucinations
Browse by: Latest US Patents, China's latest patents, Technical Efficacy Thesaurus, Application Domain, Technology Topic, Popular Technical Reports.
© 2025 PatSnap. All rights reserved.Legal|Privacy policy|Modern Slavery Act Transparency Statement|Sitemap|About US| Contact US: help@patsnap.com