Automated sectioning tomographic measurement system
a measurement system and automatic technology, applied in the field of tomography, can solve the problems of inability to accurately measure the depth of any particular step of material removal at small length scales, etc., and achieve the effect of accurate depth grinding
- Summary
- Abstract
- Description
- Claims
- Application Information
AI Technical Summary
Benefits of technology
Problems solved by technology
Method used
Image
Examples
Embodiment Construction
[0021]An embodiment of the invention is described with reference to the figures using reference designations as shown in the figures. Referring to FIG. 1, an automated tomography system is used for grinding a composite specimen attached to a robotic lifter. The lifter moves the composite specimen between an abrasion station for grinding the specimen, a wash and (optional) etch station for washing, cleaning, and / or drying the specimen, and an imaging station for imaging the specimen. The abrasion station would include an abrasive disk having a grinding surface. The abrasive disk can provide various levels of grinding such as coarse, medium, and fine grinding depending on the size of the abrasive grit used. The abrasive disk can be made of any of the various grinding media such as diamond, aluminum oxide, silicon carbide, or others. A supporting substrate of the abrasive disk can be made of various materials used for that purpose, such as commercially available polyester films, cloth,...
PUM
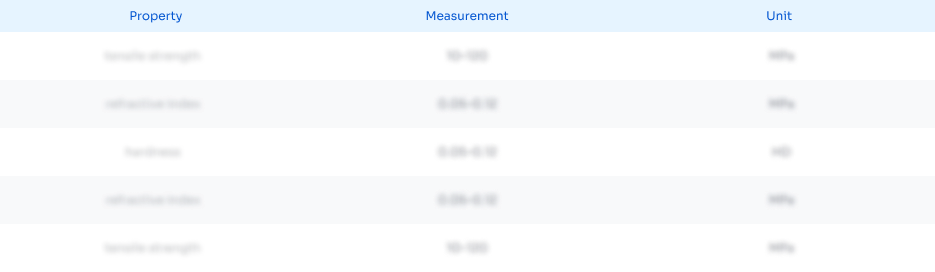
Abstract
Description
Claims
Application Information

- R&D
- Intellectual Property
- Life Sciences
- Materials
- Tech Scout
- Unparalleled Data Quality
- Higher Quality Content
- 60% Fewer Hallucinations
Browse by: Latest US Patents, China's latest patents, Technical Efficacy Thesaurus, Application Domain, Technology Topic, Popular Technical Reports.
© 2025 PatSnap. All rights reserved.Legal|Privacy policy|Modern Slavery Act Transparency Statement|Sitemap|About US| Contact US: help@patsnap.com