Intergrated Ngl Recovery and Lng Liquefaction
a technology of lng liquefaction and natural gas liquid, which is applied in the direction of refrigeration and liquidation, lighting and heating apparatus, and solidification. it can solve the problems of difficult separation of ngl, high cost of process operation, and often problematic direct liquefaction of natural gas
- Summary
- Abstract
- Description
- Claims
- Application Information
AI Technical Summary
Problems solved by technology
Method used
Image
Examples
Embodiment Construction
[0023]The inventor has discovered that C2 and C3+ components can be effectively and economically separated from natural gas in a plant (which is preferably coupled to an LNG liquefaction plant) using an absorber that operates at high pressure and produces a cryogenic pressurized lean gas, while a distillation column located downstream of an absorber operates at low pressure and produces the NGL as a bottom product and a reflux stream for the absorber. In especially preferred configurations and methods, recovery of C2 in the NGL can be adjusted by controlling process streams within the plant. Moreover, it should be appreciated that the cryogenic absorber overhead product stream is already at relatively high pressure, and energy for recompression to a pressure suitable for liquefaction is typically provided by expansion of a vapor portion of the natural gas feed stream.
[0024]In contrast, as depicted in Prior Art FIG. 1, a C2 NGL recovery plant has a single column operating at lower pr...
PUM
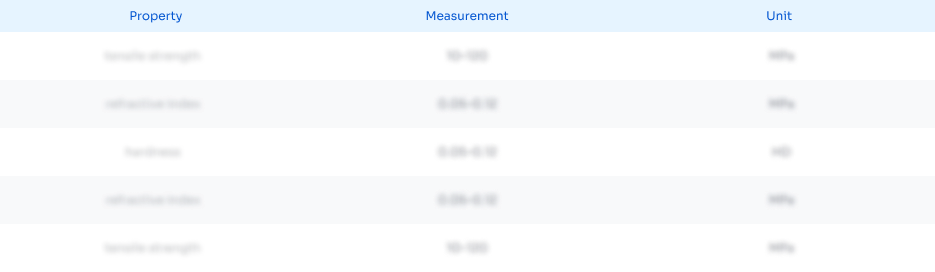
Abstract
Description
Claims
Application Information

- R&D
- Intellectual Property
- Life Sciences
- Materials
- Tech Scout
- Unparalleled Data Quality
- Higher Quality Content
- 60% Fewer Hallucinations
Browse by: Latest US Patents, China's latest patents, Technical Efficacy Thesaurus, Application Domain, Technology Topic, Popular Technical Reports.
© 2025 PatSnap. All rights reserved.Legal|Privacy policy|Modern Slavery Act Transparency Statement|Sitemap|About US| Contact US: help@patsnap.com