Production of lower molecular weight hydrocarbons
- Summary
- Abstract
- Description
- Claims
- Application Information
AI Technical Summary
Benefits of technology
Problems solved by technology
Method used
Image
Examples
example 1
[0056]The pilot scale examples were performed at a Steam Assisted Gravity Drainage (SAGD) pilot facility in the Cold Lake area of Alberta. The equipment used consisted of pumps, a pumper-mixer truck, a pressure tank, controls, instruments, and connecting pipes and hoses. The SAGD facility provided a produced water / oil emulsion input stream with an average split of 20% oil to 80% water to the pumper-mixer essentially configured as shown in FIG. 1 with the water / oil emulsion stream replacing the high molecular weight hydrocarbon source 110.
[0057]Between 9 m3 and 14 m3 of emulsion was processed in each experimental batch. The treatment was done in a continuous fashion. The Basic Solids and Water content (BS&W) of the treated oil stream ran from 1% to 5%. The solids content was less than 0.5%.
[0058]The control samples, marked Pilot Control 1, Laboratory Controls A, B, C and D were prepared to generate comparative data. Pilot Control 1 was performed in the pilot facility and the Laborato...
example 2
[0089]To further demonstrate the invention, pilot testing was performed in Lloydminster, Alberta, Canada. The oil from this region differs in composition from that used in the data reported above, i.e., from the SAGD Facility in Cold Lake.
[0090]The Lloydminster (Lloyd) pilot plant was designed on same basis and process concepts that was used at the Blackrock Cold Lake facility. Difference in the two facilities were that the Blackrock facility had a smaller capacity operation, the water / oil emulsion was already heated to 170° C., coming out of ground from a SAGD production operation, and at the Lloydminster plant the water / oil / CO2 emulsion was heated in a line-heater before was aqueous catalyst composition was blended into the emulsion stream at 95° C. to 115° C. At the Lloydminster facility, oil was trucked off and loaded into heated 1000 bbl storage tanks. The storage tanks were heated to 85° C. The approximate percent composition of the components of the catalyst precursors used i...
example 3
[0095]This examples compares four treated samples. Treated Sample 38 was treated with 2.4% of the Mix A catalyst (based dry wt. % of precursors to net weight of oil) at an emulsion temperature of 104° C. Sample 47 was treated with 1.7 wt % Mix A catalyst at an emulsion temperature of 104° C. In the treatment of both samples 38 and 47, 4.5 scft / min of CO2 was added to the emulsion. The “B” samples comprised the product of the treated Samples 47 and 38 mixed with 13% by weight of condensate. It will be noted from Table 17 below that post-treatment addition of condensate results in a dramatic difference in the end state density and viscosities in Sample 47B and 38B as compared to Samples 47 and 38.
TABLE 17Density and Viscosity of Mix A TreatedOil Samples 38, 38B, and 47, 47BSampleDensityAPIViscosity at 20 C.380.982612.431,47938B (Sample 38 plus 13 wt %0.921721.9239condensate)470.981912.517,94847B (Sample 47 plus 13 wt %0.918922.4193condensate)
[0096]Condensate can also be added initiall...
PUM
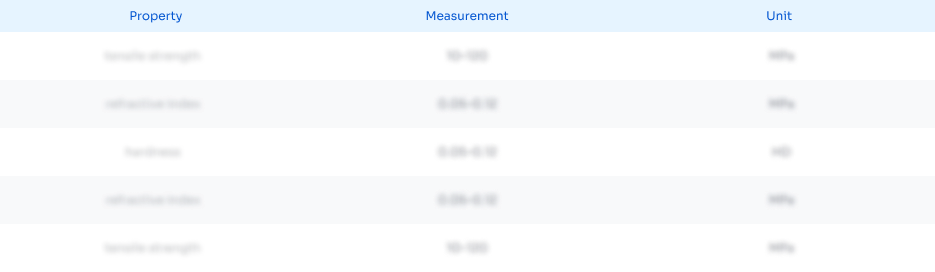
Abstract
Description
Claims
Application Information

- R&D
- Intellectual Property
- Life Sciences
- Materials
- Tech Scout
- Unparalleled Data Quality
- Higher Quality Content
- 60% Fewer Hallucinations
Browse by: Latest US Patents, China's latest patents, Technical Efficacy Thesaurus, Application Domain, Technology Topic, Popular Technical Reports.
© 2025 PatSnap. All rights reserved.Legal|Privacy policy|Modern Slavery Act Transparency Statement|Sitemap|About US| Contact US: help@patsnap.com