Method and apparatus for monitoring and control of suck back level in a photoresist dispense system
a technology of photoresist and dispense system, which is applied in the direction of liquid transfer device, liquid handling, instruments, etc., can solve the problems of insufficient volume of photoresist dispensed during coating operation, affecting the uniformity and thickness of coatings formed on the substrate, and generally affecting the film properties of photoresist, so as to achieve the effect of improving system stability
- Summary
- Abstract
- Description
- Claims
- Application Information
AI Technical Summary
Benefits of technology
Problems solved by technology
Method used
Image
Examples
Embodiment Construction
[0026]According to the present invention, techniques related to the field of semiconductor processing equipment are provided. More particularly, the present invention includes a method and apparatus for monitoring and control of fluids used to process semiconductors. Merely by way of example, the method and apparatus of the present invention have been applied to monitor and control fluids, for example photoresist, dispensed in a photolithography coating system. The method and apparatus can be applied to other processes for semiconductor substrates including chemical mechanical polishing.
[0027]FIG. 1 is a plan view of an embodiment of a track lithography tool in which the embodiments of the present invention may be used. As illustrated in FIG. 1, the track lithography tool contains a front end module 110 (sometimes referred to as a factory interface) and a process module 111. In other embodiments, the track lithography tool includes a rear module (not shown), which is sometimes refer...
PUM
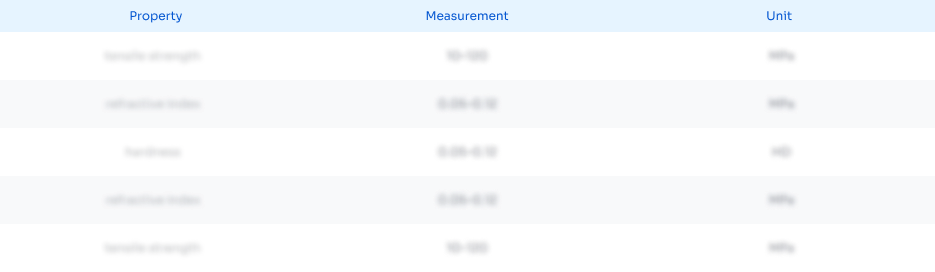
Abstract
Description
Claims
Application Information

- R&D
- Intellectual Property
- Life Sciences
- Materials
- Tech Scout
- Unparalleled Data Quality
- Higher Quality Content
- 60% Fewer Hallucinations
Browse by: Latest US Patents, China's latest patents, Technical Efficacy Thesaurus, Application Domain, Technology Topic, Popular Technical Reports.
© 2025 PatSnap. All rights reserved.Legal|Privacy policy|Modern Slavery Act Transparency Statement|Sitemap|About US| Contact US: help@patsnap.com