Plastic utility shed flooring system
- Summary
- Abstract
- Description
- Claims
- Application Information
AI Technical Summary
Benefits of technology
Problems solved by technology
Method used
Image
Examples
Embodiment Construction
[0040] While the present invention is susceptible of embodiment in various forms, there is shown in the drawings and will hereinafter be described a presently preferred embodiment with the understanding that the present disclosure is to be considered an exemplification of the invention and is not intended to limit the invention to the specific embodiments illustrated.
[0041] Referring to FIGS. 1-14, the floor assembly 100 includes a plurality of like-constructed floor panels 102. Each panel has a top surface 104, a bottom surface 106, a closed first edge 108, a second edge 110 opposite said first edge, said second edge including a first means for connecting to juxtapositioned panel members, a third edge 112 substantially perpendicular to and extending between said first and said second edges, the third edge including the first means for connecting to juxtapositioned panel members, and a fourth edge 114 opposite to and substantially parallel to said third edge, the fourth edge includ...
PUM
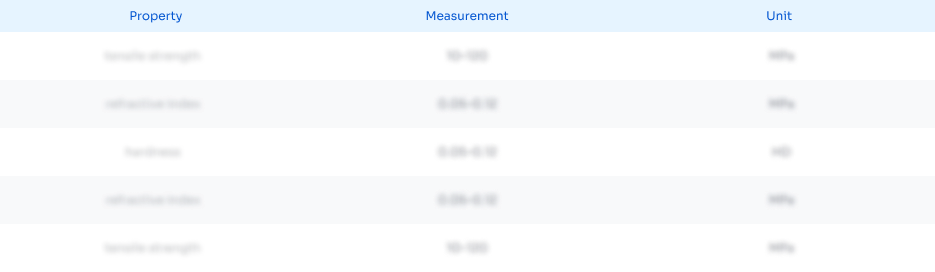
Abstract
Description
Claims
Application Information

- R&D
- Intellectual Property
- Life Sciences
- Materials
- Tech Scout
- Unparalleled Data Quality
- Higher Quality Content
- 60% Fewer Hallucinations
Browse by: Latest US Patents, China's latest patents, Technical Efficacy Thesaurus, Application Domain, Technology Topic, Popular Technical Reports.
© 2025 PatSnap. All rights reserved.Legal|Privacy policy|Modern Slavery Act Transparency Statement|Sitemap|About US| Contact US: help@patsnap.com