High density cartridge and method for reloading
a cartridge and high density technology, applied in the field of shells for use with firearms, can solve the problems of increased unintended number of waterfowl, and toxic spent lead shot to waterfowl, so as to improve lethality and patterning, reduce the payload, and improve the effect of powder charg
- Summary
- Abstract
- Description
- Claims
- Application Information
AI Technical Summary
Benefits of technology
Problems solved by technology
Method used
Image
Examples
example
[0025] Turning now to FIG. 4, the combination of the high density shot pellets 44 with the uniform smooth spherical configuration provides several advantages over all prior art hard media non-toxic, non-steel shot. The graph illustrated in FIG. 4 diagrams the a performance characteristic study of the illustrated cartridge 10 and a Hevi-Shot® cartridge. In more detail, a one and one-quarter ounce shot 18 of 129 #5 pellets 44 packed in a two and three-quarter inch 3 ft vel shell 12 with powder 14 configured to propel the shot 18 at a muzzle velocity of 1330 fps was tested against a Hevi-Shot® one and three-quarter ounce, 140 #2 pellets in a three and one-half inch 3 ft vel (1300 fps) shell, using a Remington factory load purchased commercially. The graph in FIG. 4 compares six different characteristics of these two cartridges (listed along the X-axis of the graph), each characteristic tested being listed in a column comprising side-by-side quantitative results with one being a percent...
PUM
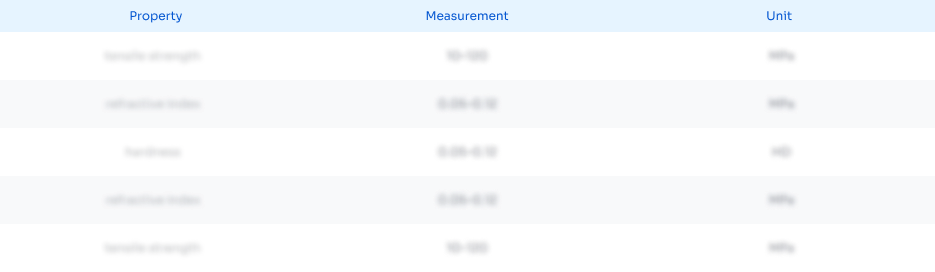
Abstract
Description
Claims
Application Information

- R&D
- Intellectual Property
- Life Sciences
- Materials
- Tech Scout
- Unparalleled Data Quality
- Higher Quality Content
- 60% Fewer Hallucinations
Browse by: Latest US Patents, China's latest patents, Technical Efficacy Thesaurus, Application Domain, Technology Topic, Popular Technical Reports.
© 2025 PatSnap. All rights reserved.Legal|Privacy policy|Modern Slavery Act Transparency Statement|Sitemap|About US| Contact US: help@patsnap.com