Wafer holder, heater unit having the wafer holder, and wafer prober having the heater unit
a technology of heater unit and heater, which is applied in the direction of electrical equipment, other accessories, packaging, etc., can solve the problems of long time between the temperature of the heater contained in the chuck and the contact failure between the wafer and the ground electrode, and improve the throughput, so as to prevent the contact failure, prevent the deformation of the chuck, and prevent the effect of temperature increas
- Summary
- Abstract
- Description
- Claims
- Application Information
AI Technical Summary
Benefits of technology
Problems solved by technology
Method used
Image
Examples
example 1a
[0157] A wafer holder 300 having the structure shown in FIG. 4 with an integral type supporter 4 was fabricated. As chuck top 2, an Si—SiC substrate having the diameter of 310 mm and thickness of 15 mm was prepared. On one surface of the substrate, a concentrical trench for vacuum chucking a wafer and a through hole were formed, and nickel plating was applied as chuck top conductive layer 3, and thus the wafer-mounting surface was formed. Thereafter, the wafer-mounting surface was polished to attain surface roughness Ra of 0.02 μm. Further, the contact surface between chuck top 2 and supporter 4 was polished and finished such that the amount of warp of the entire body was set to 10 μm and variation in thickness from the wafer-mounting surface to the contact surface with supporter 4 was set to 45 μm, and thus, chuck top 2 was completed.
[0158] Next, as supporter 4, a cylindrical plate of mullite-alumina composite having the diameter of 310 mm and the height of 40 mm was prepared. The...
example 2a
[0164] A wafer holder 400 having a separate type supporter 4 with base portion 41 and circular tube portion 42 such as shown in FIG. 5 was fabricated. First, chuck top 2 was fabricated in the similar manner as in Example 1A except that the variation in thickness of chuck top 2 from the wafer-mounting surface to the contact surface with supporter 4 was set to 46 μm.
[0165] Further, as components of supporter 4, a circular tube portion formed of a mullite-alumina composite having the diameter of 310 mm, radial thickness of 10 mm and height of 30 mm, and a base portion formed of a mullite-alumina composite having the diameter of 310 mm and thickness of 15 mm were prepared. The circular tube portion and the base portion were polished and finished such that the variation in thickness of circular tube portion 42 from the contact surface with the chuck top 2 to the contact surface with the base portion 41 attained to 22 μm, and the variation in thickness of base portion 41 from the bottom ...
example 3a
[0167] A wafer holder 400 having a separate type supporter 4 with base portion 41 and circular tube portion 42 such as shown in FIG. 5 was fabricated. Here, wafer holder 400 having a separate type supporter 4 such as shown in FIG. 5 was fabricated in the similar manner as Example 2A except that the variation in thickness of chuck top 2 from the wafer-mounting surface to the contact surface with supporter 4 was set to 9 μm, the variation in thickness of circular tube portion 42 from the contact surface with the chuck top 2 to the contact surface with the base portion 41 was set to 5 μm, and the variation in thickness of base portion 41 from the bottom surface to the contact surface with circular tube portion 42 was set to 4 μm. At this time, the variation in thickness of supporter 4 from the bottom surface to the contact surface with chuck top 2 was 10 μm.
[0168] The obtained wafer holder was mounted on a wafer prober, and semiconductor wafers were inspected continuously for 10 hours...
PUM
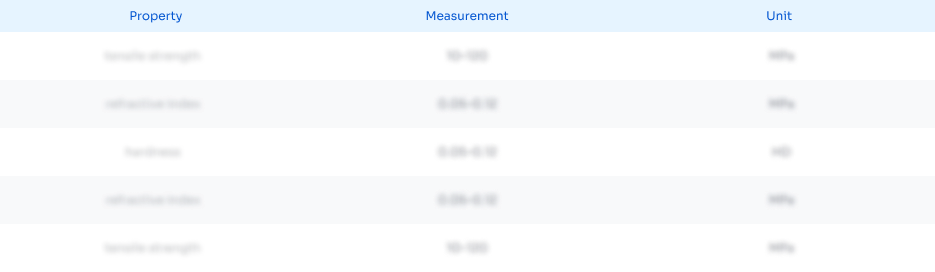
Abstract
Description
Claims
Application Information

- R&D
- Intellectual Property
- Life Sciences
- Materials
- Tech Scout
- Unparalleled Data Quality
- Higher Quality Content
- 60% Fewer Hallucinations
Browse by: Latest US Patents, China's latest patents, Technical Efficacy Thesaurus, Application Domain, Technology Topic, Popular Technical Reports.
© 2025 PatSnap. All rights reserved.Legal|Privacy policy|Modern Slavery Act Transparency Statement|Sitemap|About US| Contact US: help@patsnap.com