Reticle pod with isolation system
a technology of reticle and isolation system, which is applied in the direction of packaging goods, instruments, printing, etc., can solve the problems of unsatisfactory final products, euv photolithography reflective photomasks are susceptible to contamination and damage to a far greater degree than reticles used, and achieve enhanced shock and vibration isolation, enhanced shock and vibration absorption
- Summary
- Abstract
- Description
- Claims
- Application Information
AI Technical Summary
Benefits of technology
Problems solved by technology
Method used
Image
Examples
Embodiment Construction
[0041] References to relative terms such as upper and lower, front and back, left and right, or the like, are intended for convenience of description and are not contemplated to limit the present invention, or its components, to any one positional or special orientation. All dimensions depicted in the figures may vary with a potential design and the intended use of a specific embodiment of this invention without departing from the scope thereof.
[0042] Each of the additional figures and methods disclosed herein may be used separately, or in conjunction with other features and methods, to provide improved containers and methods for making and using the same. Therefore, combinations of features and methods disclosed herein may not be necessary to practice the invention in its broadest sense and are instead disclosed merely to particularly describe representative and preferred embodiments of the instant invention.
[0043] Referring now to FIG. 1, there is illustrated a reticle container...
PUM
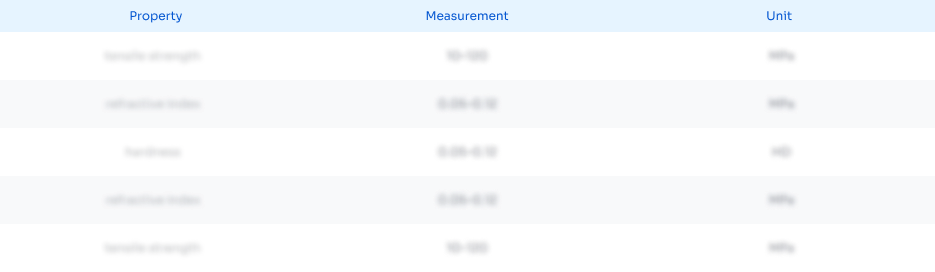
Abstract
Description
Claims
Application Information

- R&D
- Intellectual Property
- Life Sciences
- Materials
- Tech Scout
- Unparalleled Data Quality
- Higher Quality Content
- 60% Fewer Hallucinations
Browse by: Latest US Patents, China's latest patents, Technical Efficacy Thesaurus, Application Domain, Technology Topic, Popular Technical Reports.
© 2025 PatSnap. All rights reserved.Legal|Privacy policy|Modern Slavery Act Transparency Statement|Sitemap|About US| Contact US: help@patsnap.com