Seal-coated plastic container for dispensing a pressurized product
a technology for packaging and products, applied in the direction of containers, sustainable packaging industry, packaging goods types, etc., can solve the problems of reducing the shelf life of products, utilizing plastic materials to contain pressurized products, and polymeric materials such as polyolefins, etc., to achieve effective inhibition of carbon dioxide migration, low permeability, and effective inhibition of oxygen migration
- Summary
- Abstract
- Description
- Claims
- Application Information
AI Technical Summary
Benefits of technology
Problems solved by technology
Method used
Image
Examples
Embodiment Construction
[0014] Referring now to the drawings, there is illustrated a pressure resistant plastic bottle generally designated by the numeral 1 for containing and dispensing a pressurized product such as an aerosol composition. The outer surface of the plastic bottle 1 is seal coated with a layer 35 of barrier material which is composed of a polymeric material that substantially reduces the migration of carbon dioxide gas used as the propellant for the pressurized composition through the polymeric material from which the plastic bottle 1 is manufactured.
[0015] The plastic bottle 1 may be composed of any thermoplastic polymeric material that may be formed into the desired shape disclosed herein. Preferred polymeric materials include polyolefins such as polyethylene (PE) or polypropylene (PP) as well as polyesters such as polyethylene terephthalate (PET), nylons, polycarbonates, polyvinylchloride (PVC), and copolymer PVC. Examples of such materials include ethylene based polymers, including eth...
PUM
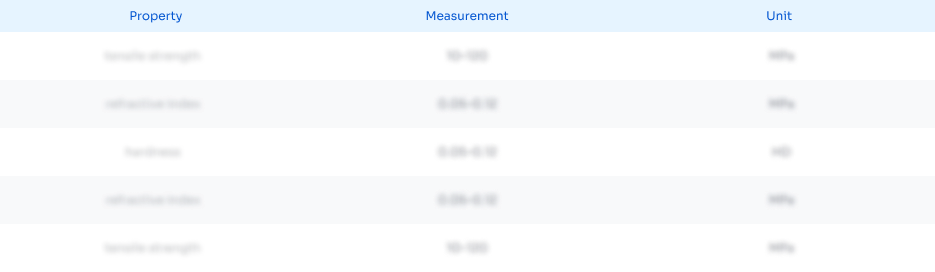
Abstract
Description
Claims
Application Information

- R&D
- Intellectual Property
- Life Sciences
- Materials
- Tech Scout
- Unparalleled Data Quality
- Higher Quality Content
- 60% Fewer Hallucinations
Browse by: Latest US Patents, China's latest patents, Technical Efficacy Thesaurus, Application Domain, Technology Topic, Popular Technical Reports.
© 2025 PatSnap. All rights reserved.Legal|Privacy policy|Modern Slavery Act Transparency Statement|Sitemap|About US| Contact US: help@patsnap.com