Hotspot spray cooling
a technology of spray cooling and thermal management system, which is applied in the direction of basic electric elements, semiconductor devices, lighting and heating apparatus, etc., can solve the problems of increasing the cost of cooling system, so as to achieve more repeatability and improve efficiency
- Summary
- Abstract
- Description
- Claims
- Application Information
AI Technical Summary
Benefits of technology
Problems solved by technology
Method used
Image
Examples
Embodiment Construction
[0038] Many of the fastening, connection, manufacturing and other means and components utilized in this invention are widely known and used in the field of the invention are described, and their exact nature or type is not necessary for a person of ordinary skill in the art or science to understand the invention; therefore they will not be discussed in detail.
[0039] Applicant hereby incorporates by reference the following U.S. patents: U.S. Pat. No. 5,220,804 for a high heat flux evaporative cooling system; and U.S. Pat. No. 5,860,602 and U.S. Pat. No. 6,016,969, each for a laminated array of pressure swirl atomizers, and U.S. Pat. No. 6,108,201 for a fluid control apparatus and method for spray cooling and U.S. patent application Ser. No. 10 / 281,391 for an actuated atomizer. Although a laminated pressure swirl atomizer array is hereby incorporated by reference and shown in the accompanying drawings, the present invention is not limited to such an apparatus, in fact, many dispensin...
PUM
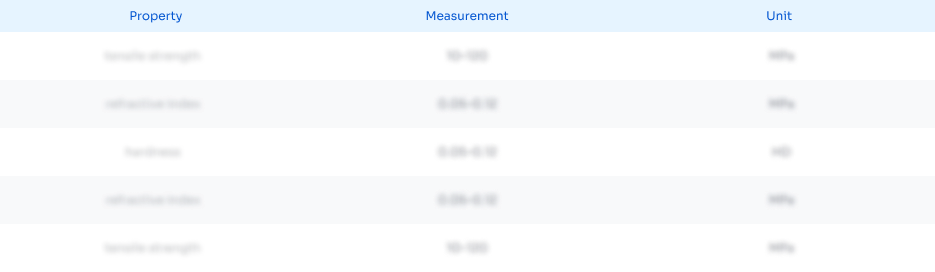
Abstract
Description
Claims
Application Information

- R&D Engineer
- R&D Manager
- IP Professional
- Industry Leading Data Capabilities
- Powerful AI technology
- Patent DNA Extraction
Browse by: Latest US Patents, China's latest patents, Technical Efficacy Thesaurus, Application Domain, Technology Topic, Popular Technical Reports.
© 2024 PatSnap. All rights reserved.Legal|Privacy policy|Modern Slavery Act Transparency Statement|Sitemap|About US| Contact US: help@patsnap.com