Multi-spectral laser array and optical system
a laser array and optical system technology, applied in the field of electronic display and printing systems, can solve the problems of system sensitive to the potential failure of the laser source, limited development of laser projection systems, and typically intended to be multi-color,
- Summary
- Abstract
- Description
- Claims
- Application Information
AI Technical Summary
Benefits of technology
Problems solved by technology
Method used
Image
Examples
Embodiment Construction
[0045] A schematic of a vertical cavity organic laser structure 10 is shown in FIG. 1. The substrate 20 can either be light transmissive or opaque, depending on the intended direction of optical pumping and laser emission. Light transmissive substrates 20 may be transparent glass, plastic, or other transparent materials such as sapphire. Alternatively, opaque substrates including, but not limited to, semiconductor material (e.g. silicon) or ceramic material may be used in the case where both optical pumping and emission occur through the same surface. On the substrate is deposited a bottom dielectric stack 30 followed by an organic active region 40. A top dielectric stack 50 is then deposited. The organic laser film structure 35 comprises the combination of the bottom dielectric stack 30, the organic active region 40, and the top dielectric stack 50. A pump light source 65 provides a pump beam 60 that optically pumps the vertical cavity organic laser structure 10. The source of the ...
PUM
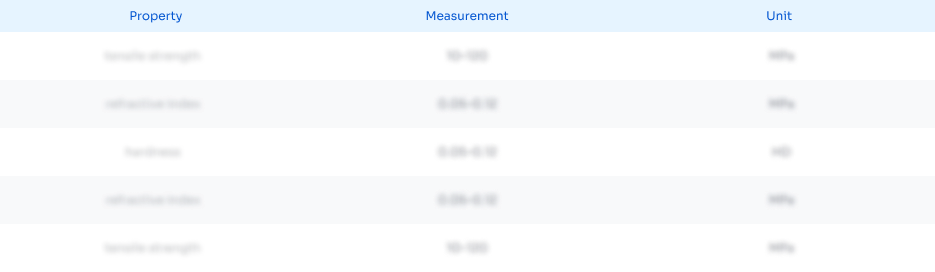
Abstract
Description
Claims
Application Information

- R&D
- Intellectual Property
- Life Sciences
- Materials
- Tech Scout
- Unparalleled Data Quality
- Higher Quality Content
- 60% Fewer Hallucinations
Browse by: Latest US Patents, China's latest patents, Technical Efficacy Thesaurus, Application Domain, Technology Topic, Popular Technical Reports.
© 2025 PatSnap. All rights reserved.Legal|Privacy policy|Modern Slavery Act Transparency Statement|Sitemap|About US| Contact US: help@patsnap.com