Thermosyphon and method for producing it
a technology of thermosyphon and thermosyphon plate, which is applied in the direction of heat exchange apparatus, electric devices, solid-state devices, etc., can solve the problems of difficult and time-consuming manufacturing techniques, limited cooling efficiency of this type of thermosyphon plate,
- Summary
- Abstract
- Description
- Claims
- Application Information
AI Technical Summary
Benefits of technology
Problems solved by technology
Method used
Image
Examples
example
[0024] A lid is extruded from an aluminium billet so that a plate is formed having fins extending from one side along the centre of the plate. The fins extending beyond the area dedicated to the evaporator are removed by milling to form the evaporator section, E, according to FIG. 2a. A base is then extruded to form a plate having heat dissipating fins extending from one side. The flat side of the base is machined so that condenser channels, A, are formed in a pattern according to FIG. 2a as well as a cavity for the evaporator fins to fit into. The lid is joined to the base by traversing a friction stir welding tool along the joint (shown as the contour of the thermosyphon in FIG. 1a). When the lid and the base are joined a sealed chamber constituting a thermosyphon is formed inside the chamber. The evaporator is filled with liquid. The choice of working fluid is based upon the working temperature of the thermosyphon, and may be chosen according to the specific demands in each case....
PUM
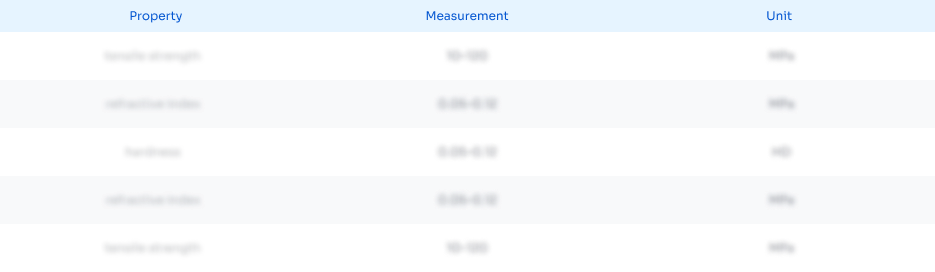
Abstract
Description
Claims
Application Information

- R&D
- Intellectual Property
- Life Sciences
- Materials
- Tech Scout
- Unparalleled Data Quality
- Higher Quality Content
- 60% Fewer Hallucinations
Browse by: Latest US Patents, China's latest patents, Technical Efficacy Thesaurus, Application Domain, Technology Topic, Popular Technical Reports.
© 2025 PatSnap. All rights reserved.Legal|Privacy policy|Modern Slavery Act Transparency Statement|Sitemap|About US| Contact US: help@patsnap.com