Hydrocarbon gas processing
a technology of hydrocarbon gas and processing method, which is applied in the direction of cold treatment separation, liquefaction, solidification, etc., can solve the problems of not only the capital cost of the plant, but also the operating expense of the plant, and the substantial incremental cost of operating in this manner
- Summary
- Abstract
- Description
- Claims
- Application Information
AI Technical Summary
Benefits of technology
Problems solved by technology
Method used
Image
Examples
Embodiment Construction
. 3 and 4 illustrate flow diagrams of a process in accordance with the present invention. The feed gas composition and conditions considered in the inventive process are the same as those in prior art FIGS. 1 and 2 and comprises a similar cryogenic expansion recovery process. Accordingly, the FIGS. 3 / 4 process can be compared with that of the FIGS. 1 and 2 processes to illustrate the operation of the present invention. The FIGS. 3 / 4 process described below is exemplary of the present invention and is not intended to limit the invention claimed herein. In particular, one skilled in the art will realize that many variations on the demethanizer deethanizer configuration and the various energy exchanges illustrated exist which are compatible with and included within the scope of the claimed invention. In the simulation of the FIG. 3 process, inlet gas (stream 1) enters at 50.degree. F. and a pressure of 650 psia. The feed stream 1 is split into streams 2 and 3. Stream 2 is subsequently ...
PUM
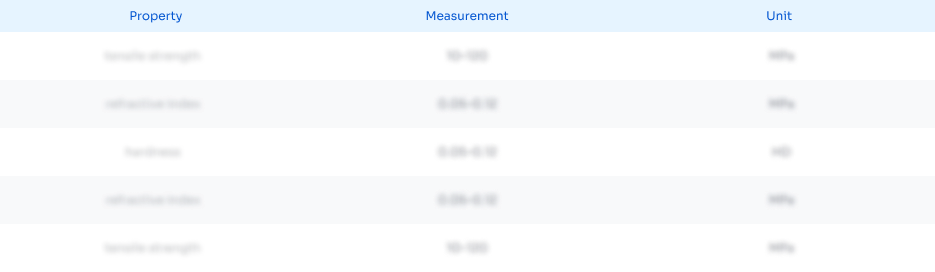
Abstract
Description
Claims
Application Information

- R&D
- Intellectual Property
- Life Sciences
- Materials
- Tech Scout
- Unparalleled Data Quality
- Higher Quality Content
- 60% Fewer Hallucinations
Browse by: Latest US Patents, China's latest patents, Technical Efficacy Thesaurus, Application Domain, Technology Topic, Popular Technical Reports.
© 2025 PatSnap. All rights reserved.Legal|Privacy policy|Modern Slavery Act Transparency Statement|Sitemap|About US| Contact US: help@patsnap.com