Dead zone compensating method for space vector pulse width modulating output
A technology of dead zone compensation and pulse width modulation, which is applied in the field of AC servo, can solve the problems of poor low-speed performance of AC servo system, dead zone effect of AC servo system, and inability to guarantee the minimum speed, etc., to achieve easy implementation and overcome output dead zone effect, the effect of eliminating torque ripple
- Summary
- Abstract
- Description
- Claims
- Application Information
AI Technical Summary
Problems solved by technology
Method used
Image
Examples
Embodiment Construction
[0025] In a modern all-digital AC servo system, the voltage source inverter is generally driven by PWM (pulse width modulation) technology to realize the sine wave control of the AC permanent magnet synchronous motor. The voltage source inverter is composed of six high-power switch-type power electronic devices, which are composed of three-way bridge arms in groups of two. When working, the upper and lower bridge arms are turned on in turn and cannot be turned on at the same time. According to the characteristics of high-power power electronic devices, the turn-off time is longer than the turn-on time. In order to prevent the straight-through of the upper and lower bridge arms, when designing the SVPWM (space vector pulse width modulation) signal, it is necessary to ensure that the device to be turned on lags behind the device to be turned off by a dead time T d , which causes the dead zone effect, which causes the current output from the inverter to the AC permanent magnet s...
PUM
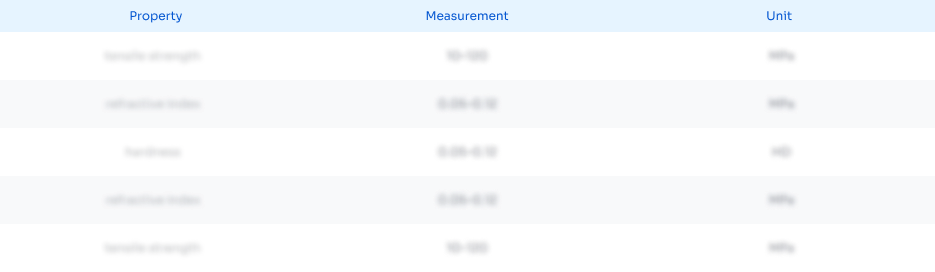
Abstract
Description
Claims
Application Information

- R&D Engineer
- R&D Manager
- IP Professional
- Industry Leading Data Capabilities
- Powerful AI technology
- Patent DNA Extraction
Browse by: Latest US Patents, China's latest patents, Technical Efficacy Thesaurus, Application Domain, Technology Topic, Popular Technical Reports.
© 2024 PatSnap. All rights reserved.Legal|Privacy policy|Modern Slavery Act Transparency Statement|Sitemap|About US| Contact US: help@patsnap.com