Wastegas steam turbine super charging system
A technology of steam turbine and supercharging system, applied in exhaust devices, mechanical equipment, engine components, etc., can solve problems such as increased fuel consumption, supercharger burst, increased oil seal burden, etc., to reduce oil consumption rate, The effect of reducing fuel consumption and improving thermal efficiency
- Summary
- Abstract
- Description
- Claims
- Application Information
AI Technical Summary
Problems solved by technology
Method used
Image
Examples
Embodiment Construction
[0032] In an embodiment, as shown in the figure, the gas-steam turbocharging system includes a compressor 2 connected to the intake pipe 34 of the diesel engine 1 and a heat exchange device connected to the exhaust pipe 4 of the diesel engine 1. The heat exchange device includes one The shell 31 communicating with the exhaust pipe 4 and the heat exchanger, the superheated steam generator 3, and the air storage chamber 7 arranged in the shell, the superheated steam generator 3 and the air storage chamber 7 are located on the top of the heat exchanger, The heat exchanger includes a first heat exchanger 8, a second heat exchanger 9, a third heat exchanger 10, a fourth heat exchanger 11, and a fifth heat exchanger 12 separately arranged. The first heat exchanger The air chamber of 8 communicates with the air chamber of the second heat exchanger 9 through an inhalation air machine 27 arranged below the heat exchanger.
[0033] The superheated steam generator 3 is a serpentine tube comm...
PUM
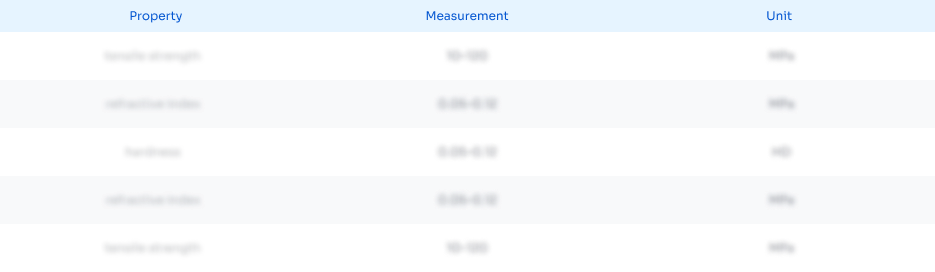
Abstract
Description
Claims
Application Information

- R&D Engineer
- R&D Manager
- IP Professional
- Industry Leading Data Capabilities
- Powerful AI technology
- Patent DNA Extraction
Browse by: Latest US Patents, China's latest patents, Technical Efficacy Thesaurus, Application Domain, Technology Topic, Popular Technical Reports.
© 2024 PatSnap. All rights reserved.Legal|Privacy policy|Modern Slavery Act Transparency Statement|Sitemap|About US| Contact US: help@patsnap.com