Continuous colloid mixer and its application
A mixer and colloid technology, applied in mixers, applications, mixers with rotary stirring devices, etc., can solve the problem of not realizing the continuous preparation process of catalysts, not suitable for continuous online mixing to prepare colloids, and not continuous automatic production of cracking catalysts process and other problems, to achieve the effect of reducing production cost and labor intensity, reducing dust loss and improving production environment
- Summary
- Abstract
- Description
- Claims
- Application Information
AI Technical Summary
Problems solved by technology
Method used
Image
Examples
Embodiment 1
[0050] In this embodiment, the mixer provided by the present invention is used to uniformly mix the solid powder and the liquid to prepare a colloid.
[0051] The structure of the mixer is shown in Figure 1: the inner diameter of the mixer shell is 200mm, the height of the shell is 350mm, the tooth height of the stator 3 and rotor 4 of the mixer is 10mm, both the stator 3 and the rotor 4 are composed of three layers of teeth, each layer There are 16 teeth, the gap between the stator teeth 6 and the rotor teeth 7 from the center of the shaft t1 = 4mm, t2 = 3.5mm, t3 = 3mm, t4 = 2.5mm, t5 = 2.4mm, scraper 14 from the device The distance between the walls is d1=d2=d3=2mm, the installation angle of the scraper 14 is α=20°, and the power of the motor is 2.5KW. In this embodiment, kaolin is mixed with deionized water. Kaolin is imported from solid feed pipe 1, and deionized water is imported from liquid feed pipe 2. The colloid treatment capacity is 300kg / h, and the production collo...
Embodiment 2
[0056] In this embodiment, the mixer provided by the present invention is used to uniformly mix two colloids with relatively high viscosity to prepare a colloid.
[0057] The size of the mixer shell remains unchanged, and the internal stator 3 and rotor 4 are replaced. Both the stator 3 and the rotor 4 are composed of two layers of teeth. The stator teeth 6 and the rotor teeth 7 each have 12 teeth, and the tooth height is 10mm. The gap between the teeth 6 and the rotor teeth 7 is t1=4mm, t2=3.5mm, t3=3mm, the distance between the scraper 14 and the wall is d1=d2=d3=2mm, and the installation angle of the scraper 14 is α=20 °; 45% of solid content kaolin colloid and 14% of solid content of pseudoboehmite colloid are mixed with 10:15 to prepare colloid, the stirring motor power is 3.8KW, the production colloid 400kg, the colloid solid content is 26.4%, the colloid The particle size is 0.5-4μm, the average particle size of the colloid is 1.6μm, requires 2-3 people to operate the s...
Embodiment 3
[0062] This example is a specific implementation method of applying the continuous colloid mixer provided by the present invention to the continuous production of cracking catalysts.
[0063] The specific steps of continuous production of cracking catalyst are as follows:
[0064] a) Kaolin, pseudo-boehmite, and molecular sieve DASY2.0 powder raw materials are mechanically crushed into fine powders with an average particle size of less than 200 μm; the solid powder is accurately measured online and continuously transported to the facility described in Example 1 with a screw conveyor in the mixer;
[0065] b) Kaolin powder, deionized water, and aluminum sol are quickly mixed to produce kaolin colloid (colloid 1), with a solid content of 40%;
[0066] Pseudo-boehmite powder is quickly mixed with deionized water and hydrochloric acid to produce pseudo-boehmite colloid (colloid 2), with a solid content of 15%;
[0067] Molecular sieve DASY2.0 and deionized water are quickly mixe...
PUM
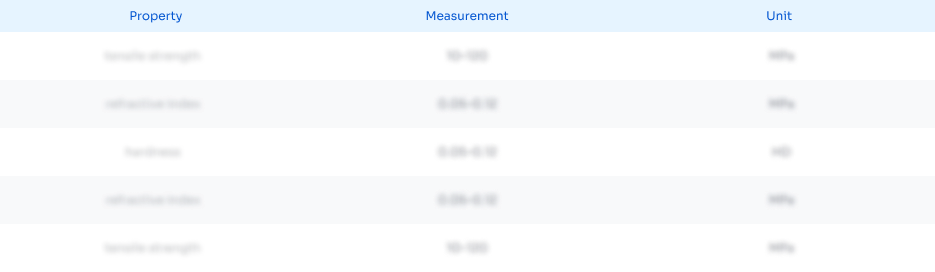
Abstract
Description
Claims
Application Information

- R&D
- Intellectual Property
- Life Sciences
- Materials
- Tech Scout
- Unparalleled Data Quality
- Higher Quality Content
- 60% Fewer Hallucinations
Browse by: Latest US Patents, China's latest patents, Technical Efficacy Thesaurus, Application Domain, Technology Topic, Popular Technical Reports.
© 2025 PatSnap. All rights reserved.Legal|Privacy policy|Modern Slavery Act Transparency Statement|Sitemap|About US| Contact US: help@patsnap.com