Polyphenylether modified phenolic resin, and its preparing method
A technology of phenolic resin and polyphenylene ether, which is applied in the field of polyphenylene ether modified phenolic resin and its preparation, can solve problems such as high friction coefficient, phenolic resin does not have self-lubricating effect, and mechanical wear of materials, so as to achieve excellent mechanical properties, Effects of improving mildew resistance, insulation, and impact resistance
- Summary
- Abstract
- Description
- Claims
- Application Information
AI Technical Summary
Problems solved by technology
Method used
Image
Examples
Embodiment 1
[0027] a: Add 10 parts of modifier X to phenol under stirring condition, and make it dissolve in phenol;
[0028] b: After fully dissolving, add 10 parts of polyphenylene ether under stirring condition;
[0029] c: add 40 parts of solid paraformaldehyde again;
[0030] d: Add 10 polysulfone under stirring condition;
[0031] e: Add 94 parts of ethanol solvent in the reactor to dilute the resin, and add 2 parts of sodium pentachlorophenate;
[0032] f: Evenly impregnate 55 parts of glass fiber into the above resin after coupling treatment;
[0033] g: Dry the impregnating material so that the water and volatile matter content is 2-5%;
[0034] h: After-baking the toughened phenolic molding compound;
[0035] i: The impregnating material is cut into pellets on a pelletizer and molded.
Embodiment 2
[0037] a: Add 15 parts of modifier X to 100 parts of phenol under stirring condition, and make it dissolve in phenol;
[0038] b: After fully dissolving, 15 parts of polyphenylene ether under stirring conditions;
[0039] c: add 45 parts of solid paraformaldehyde again;
[0040] d: Add 20 parts of polysulfone under stirring condition;
[0041] e: Add 100 parts of acetone dissolving agent in the reactor to dilute the resin, and add 5 parts of sodium pentachlorophenate;
[0042] f: Evenly impregnate 60 parts of cotton cloth in the above resin after coupling treatment;
[0043] g: Dry the impregnating material so that the water and volatile matter content is 2-5%;
[0044] h: After-baking the toughened phenolic molding compound;
[0045] i: The impregnating material is cut into pellets on a pelletizer and molded.
Embodiment 3
[0047] a: Add 12 parts of modifier X to phenol under stirring condition, and make it dissolve in phenol;
[0048] b: After fully dissolving, add 12 parts of polyphenylene ether under stirring condition;
[0049] c: add 43 parts of solid paraformaldehyde again;
[0050] d: Add 15 parts of polysulfone under stirring condition;
[0051] e: Add 97 parts of solvent acetone in the reactor to dilute the resin, and add 3 parts of sodium pentachlorophenate;
[0052] f: Evenly impregnate 57 parts of cotton fibers in the above resin after coupling treatment;
[0053] g: Dry the impregnating material so that the water and volatile matter content is 2-5%;
[0054] h: After-baking the toughened phenolic molding compound;
[0055] i: The impregnating material is cut into pellets on a pelletizer and molded.
[0056] In the above embodiments, the size of the diced impregnation material is about 15-25mm or oriented at 1600-1800mm. The molding temperature is 160±5°C, the molding pressure i...
PUM
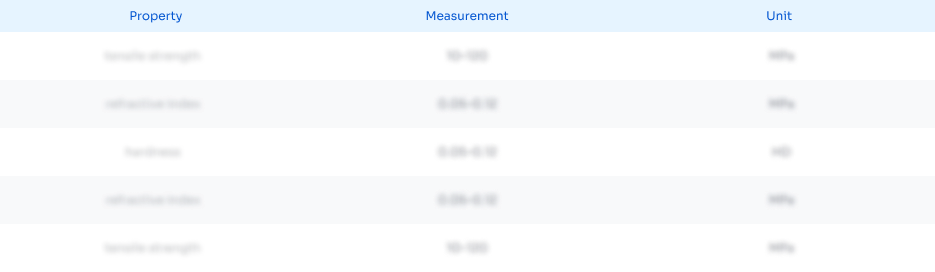
Abstract
Description
Claims
Application Information

- R&D
- Intellectual Property
- Life Sciences
- Materials
- Tech Scout
- Unparalleled Data Quality
- Higher Quality Content
- 60% Fewer Hallucinations
Browse by: Latest US Patents, China's latest patents, Technical Efficacy Thesaurus, Application Domain, Technology Topic, Popular Technical Reports.
© 2025 PatSnap. All rights reserved.Legal|Privacy policy|Modern Slavery Act Transparency Statement|Sitemap|About US| Contact US: help@patsnap.com