Surface treatment process for iron-base sintered metal piece
An iron-based powder metallurgy and surface treatment technology, which is applied in the direction of metal material coating process, coating, hot-dip plating process, etc., can solve the problems of high production cost, poor applicability, polluted plating solution, etc., and achieve good surface integrity , Improve the density, the effect of strong feasibility
- Summary
- Abstract
- Description
- Claims
- Application Information
AI Technical Summary
Problems solved by technology
Method used
Image
Examples
Embodiment 1
[0015] Dry the iron-based powder metallurgy parts at 400°C for half an hour to remove oil (grease), then use 20% (mass percentage, the same below) hydrochloric acid solution for derusting treatment, and wash with cold water after derusting. Boil the workpiece treated above for 10 minutes to eliminate the cleaning solution that may remain inside the workpiece during the degreasing and rust removal process. The boiled workpiece uses 25% ZnCl 2 with NH 4 Cl mixed solution for soaking, in which ZnCl 2 with NH 4 The mass ratio of Cl was 1:3. After soaking for 2 minutes, the powder metallurgy parts were taken out and dried at 180°C for 20 minutes. After the workpiece is dried, it can be immersed in the pure zinc liquid, and the workpiece is dipped in the pure zinc liquid for 1 minute to obtain a 30 micron thick hot-dip galvanized layer. According to metallographic analysis, the micropores of the powder metallurgy parts after hot-dip galvanizing are obviously reduced, and the den...
Embodiment 2
[0017] Use alkaline detergent to remove oil (grease) from iron-based powder metallurgy parts, then use 20% hydrochloric acid solution to remove rust, and wash with cold water after rust removal. Boil the workpiece treated above for 10 minutes to eliminate the cleaning solution that may remain inside the workpiece during the degreasing and rust removal process. The boiled workpiece uses 35% ZnCl 2 with NH 4 Cl mixed solution for soaking, in which ZnCl 2 with NH 4 The mass ratio of Cl was 1:3. After soaking for 2 minutes, the powder metallurgy parts were taken out and dried at 150°C for 30 minutes. After the workpiece is dried, it can be immersed in the pure zinc liquid, and the workpiece is dipped in the pure zinc liquid for 2 minutes to obtain a 90 micron thick hot-dip galvanized layer. According to metallographic analysis, the micropores of the powder metallurgy parts after hot-dip galvanizing are obviously reduced, and the density is increased by 1.6%. Figure 1 is an op...
Embodiment 3
[0019] Dry the iron-based powder metallurgy parts at 350°C for half an hour to remove oil (grease), then use 20% hydrochloric acid solution for rust removal, and wash with cold water after rust removal. Boil the workpiece treated above for 10 minutes to eliminate the cleaning solution that may remain inside the workpiece during the degreasing and rust removal process. The boiled workpiece was painted with 8% potassium fluozirconate aqueous solution, and then the powder metallurgy piece was taken out and dried at 350° C. for 30 minutes. After the workpiece is dried, it can be immersed in the pure aluminum liquid, and the workpiece is dip-coated in the pure aluminum liquid for 1 minute to obtain a 30-micron thick hot-dip aluminum layer. According to metallographic analysis, the micropores of the powder metallurgy parts after hot-dip aluminum plating are obviously reduced, and the density is increased by 0.8% at the same time.
PUM
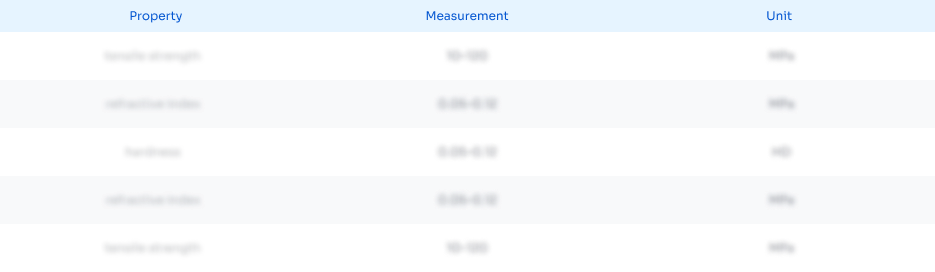
Abstract
Description
Claims
Application Information

- R&D
- Intellectual Property
- Life Sciences
- Materials
- Tech Scout
- Unparalleled Data Quality
- Higher Quality Content
- 60% Fewer Hallucinations
Browse by: Latest US Patents, China's latest patents, Technical Efficacy Thesaurus, Application Domain, Technology Topic, Popular Technical Reports.
© 2025 PatSnap. All rights reserved.Legal|Privacy policy|Modern Slavery Act Transparency Statement|Sitemap|About US| Contact US: help@patsnap.com