A thermal spraying preprocessing method and a cylinder block of an engine so preprocessed
A technology of engine cylinder and thermal spraying, which is applied in the direction of fusion spraying, honing machine tools, coating of superimposed layers, etc., which can solve the problems of rough surface of the substrate, weak resistance, and reduced reliability of thermal sprayed coatings, etc.
- Summary
- Abstract
- Description
- Claims
- Application Information
AI Technical Summary
Problems solved by technology
Method used
Image
Examples
Embodiment Construction
[0022] A description will now be given with reference to an embodiment of the method. While the claims are not limited to these examples, an appreciation of various aspects of the method is best obtained through a discussion of various examples of the method.
[0023] The manner in which the method is carried out is explained with reference to the accompanying drawings.
[0024] Fig. 1 is an explanatory diagram illustrating a series of processes of casting, roughening, and thermal spraying. As shown in FIG. 1, first, the inner surface of the cylinder block is formed by casting. Thereafter, the inner surface is roughened by the method described below, and then material is thermally sprayed onto the roughened surface.
[0025] FIG. 2 is a cross-sectional view of a processing roll inserted into a workpiece W, illustrating thermal spray pretreatment according to a first embodiment of the method.
[0026] This thermal spraying pretreatment method uses a working roller 3 made of ...
PUM
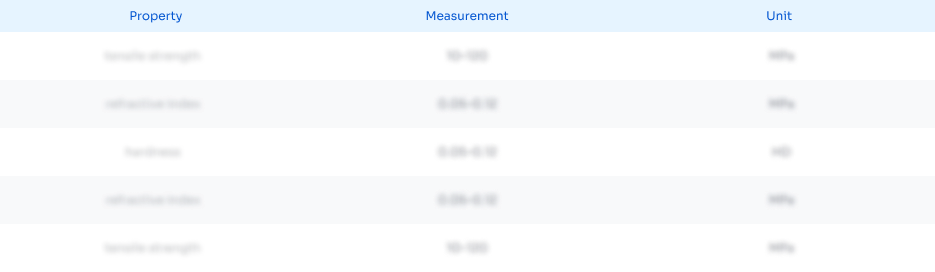
Abstract
Description
Claims
Application Information

- R&D Engineer
- R&D Manager
- IP Professional
- Industry Leading Data Capabilities
- Powerful AI technology
- Patent DNA Extraction
Browse by: Latest US Patents, China's latest patents, Technical Efficacy Thesaurus, Application Domain, Technology Topic, Popular Technical Reports.
© 2024 PatSnap. All rights reserved.Legal|Privacy policy|Modern Slavery Act Transparency Statement|Sitemap|About US| Contact US: help@patsnap.com