Process for separation and production of titanium-rich materials from titanium-containing blast furnace slag
A technology for blast furnace slag and titanium-rich material, which is applied in the field of separating and producing titanium-rich material from titanium-containing blast furnace slag, can solve the problems of poor effect, difficult to control cooling rate, long oxidation time, etc., and achieves reasonable process design and thermal energy utilization. High efficiency, practical and simple equipment
- Summary
- Abstract
- Description
- Claims
- Application Information
AI Technical Summary
Problems solved by technology
Method used
Image
Examples
Embodiment approach 1
[0049] Embodiment 1 (Adjust the corresponding content in the following embodiments according to the modification of the claims)
[0050] Weigh 200g of titanium-containing blast furnace slag, whose composition is 24.79%TiO 2 , 20.14% CaO, 8.89% MgO, 13.86% Al 2 o 3 , 3.10% FeO, 5.89% MFe and 18.60% SiO 2 . Put the weighed titanium slag in the slag pot, heat and melt it, spray flammable gas into the slag, and adjust the temperature of the slag at about 1400°C; when the temperature is constant, add 4g of additive CaO to the slag in the slag pot , while (or after) adding the additive, blow air into the slag, the oxidation time is 5min, and the partial pressure of oxygen is 1-10 2 In the kPa range, the titanium component is selectively enriched in the perovskite phase. After that, the temperature of the slag increases by about 30°C due to oxidation, reaching 1430°C; the cooling rate is controlled at 2°C / min in the temperature range of 1430-1100°C, and the perovskite phase grow...
Embodiment approach 2
[0052] Weigh 200g of titanium-containing blast furnace slag, whose composition is 24.79%TiO 2 , 20.14% CaO, 8.89% MgO, 13.86% Al 2 o 3 , 3.10% FeO, 5.89% MFe and 18.60% SiO 2 . Put the weighed titanium slag in the slag tank, heat it with resistance to melt the slag, spray flammable gas into the slag, adjust the temperature of the slag to 1400C, keep the temperature constant, let air in the molten state, and add additives at the same time CaO 8g, oxidation time 5min, oxygen partial pressure in 1-10 2 Within the range of kPa; after oxidation, the temperature of the slag rises to 1420°C, and the temperature is lowered within the temperature range of 1420-1100°C, and the cooling rate is 2°C / min; the cooled oxidized slag is crushed and ground, and the particle size is +100 mesh~- 200 mesh, after re-election, flotation, and discharge of tailings, 40.3% TiO 2 In addition, 7.8g of metallic iron microspheres were deposited at the bottom of the slag tank, and were separated by magn...
Embodiment approach 3
[0054] Weigh 200g of titanium-containing blast furnace slag, whose composition is 24.79%TiO 2 , 20.14% CaO, 8.89% MgO, 3.86% Al 2 o 3 , 3.10% FeO, 5.89% MFe and 18.60% SiO 2 . Put the weighed titanium slag in the slag tank, heat the slag with resistance to melt, spray flammable gas into the slag, adjust the temperature of the slag to 1400°C, keep the temperature constant, feed oxygen in the molten state, and add additives at the same time CaO 8g, oxidation time 5min, oxygen partial pressure in 1-10 2 In the kPa range, the slag temperature rises to 1450°C after oxidation. The temperature is lowered within the temperature range of 1450-1100°C, and the cooling rate is 2.0°C / min. After cooling, the oxidized condensate is crushed and ground to a particle size of +100 mesh to -200 mesh. After gravity separation and flotation, the tailings are discarded to obtain 41.8% TiO 2 of titanium-rich concentrates. In addition, 8.5g of metallic iron microspheres were deposited on the bo...
PUM
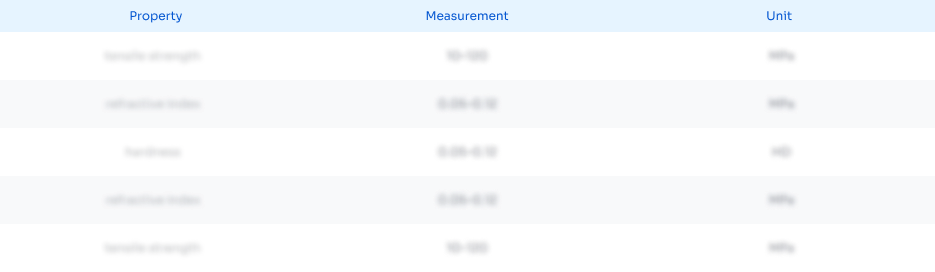
Abstract
Description
Claims
Application Information

- R&D
- Intellectual Property
- Life Sciences
- Materials
- Tech Scout
- Unparalleled Data Quality
- Higher Quality Content
- 60% Fewer Hallucinations
Browse by: Latest US Patents, China's latest patents, Technical Efficacy Thesaurus, Application Domain, Technology Topic, Popular Technical Reports.
© 2025 PatSnap. All rights reserved.Legal|Privacy policy|Modern Slavery Act Transparency Statement|Sitemap|About US| Contact US: help@patsnap.com