Laser deposited nickel-base alloy powder
A nickel-based alloy and laser cladding technology, which is applied in the direction of heating inorganic powder coating, etc., can solve the problems of inability to effectively adjust the tensile stress of the cladding layer, and achieve the effects of offsetting tensile stress, reducing sensitivity, and offsetting volume shrinkage
- Summary
- Abstract
- Description
- Claims
- Application Information
AI Technical Summary
Problems solved by technology
Method used
Image
Examples
Embodiment 1
[0018] Example 1. Laser cladding of a high-hardness nickel-based alloy on the surface of a carbon steel substrate, and adding CuAlO, a material with a negative thermal expansion coefficient, to the cladding alloy 2 Composition of Al 2 o 3 , Cu.
[0019] Press Al 2 o 3 Weigh 1-5% Al by weight of nickel-based alloy with a molar ratio of 1:2 to Cu 2 o 3 and Cu are added to the nickel-based alloy powder, and mixed by ball milling for 60-120 minutes. Grind and clean the metal substrate to be clad, and use acetate fiber + acetone adhesive or other organic adhesives to mix and bond the alloy powder after ball milling on the metal substrate. The coating thickness is 1.0-1.2mm, and air-dried After that, laser cladding is carried out, and the process parameters of laser cladding treatment: laser wavelength 10.6μm, power density 2.0-3.0kW / cm 2 , beam scanning speed 3-6mm / s. After testing and analysis, it is found that the macroscopic appearance of the laser cladding layer is flat...
Embodiment 2
[0020] Example 2: Laser cladding of a high-hardness nickel-based alloy on the surface of a carbon steel substrate, and adding ZrV, a material with a negative thermal expansion coefficient, to the cladding alloy 2 o 7 The composition element ZrO 2 , V 2 o 5 .
[0021] Press ZrO 2 with V 2 o 5 Molar ratio 1:1 Weigh 1-10% ZrO by nickel-based alloy weight 2 and V 2 o 5 , add nickel-based alloy powder, ball mill and mix for 60-120 minutes, grind and wash the metal substrate to be clad, and use acetate fiber + acetone adhesive or other organic adhesive to mix and bond the alloy powder after ball milling On the metal substrate, the thickness of the coating is 1.0-1.2mm. After air-drying, laser cladding is carried out. Laser cladding process parameters: laser wavelength 10.6μm, power density 2.0-3.0kW / cm 2 , beam scanning speed 3-6mm / s. After testing and analysis, it is found that the macroscopic appearance of the laser cladding layer is flat, smooth, uniform, dense and fre...
Embodiment 3
[0022] Example 3: Laser cladding of a high-hardness nickel-based alloy on the surface of a carbon steel substrate, adding ZrW, a material with a negative thermal expansion coefficient, to the cladding alloy 2 o 8 Composition element WO 3 , ZrO 2 .
[0023] Press ZrO 2 with WO 3 ZrO with a molar ratio of 1:2 weighing 1-10% of the nickel-based alloy weight 2 with WO 3 , add nickel-based alloy powder, ball mill and mix for 60-120 minutes, grind and clean the metal substrate to be clad, and mix and bond the alloy powder after ball milling with cellulose acetate + acetone adhesive or other organic adhesive On the metal substrate, the thickness of the coating is 1.0-1.2mm. After air-drying, laser cladding is carried out. Laser cladding process parameters: laser wavelength 10.6μm, power density 2.0-3.0kW / cm 2 , beam scanning speed 3-6mm / s. After testing and analysis, it is found that the macroscopic morphology of the laser cladding layer is slightly worse than the above two e...
PUM
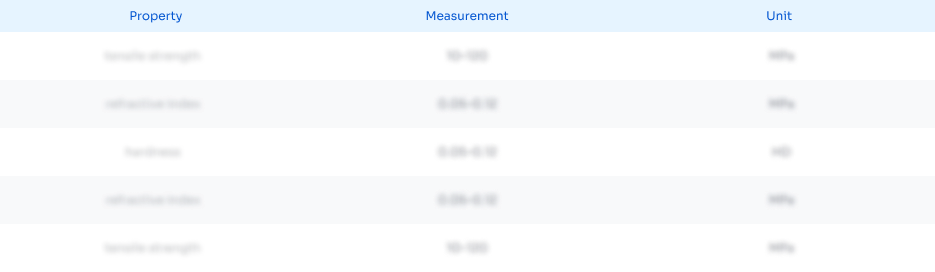
Abstract
Description
Claims
Application Information

- R&D
- Intellectual Property
- Life Sciences
- Materials
- Tech Scout
- Unparalleled Data Quality
- Higher Quality Content
- 60% Fewer Hallucinations
Browse by: Latest US Patents, China's latest patents, Technical Efficacy Thesaurus, Application Domain, Technology Topic, Popular Technical Reports.
© 2025 PatSnap. All rights reserved.Legal|Privacy policy|Modern Slavery Act Transparency Statement|Sitemap|About US| Contact US: help@patsnap.com