Composite coloration method of aluminium anode oxide film
A composite coloring, aluminum anode technology, used in electrolytic coatings, surface reaction electrolytic coatings, coatings, etc., can solve the problems of monotonous color, poor light resistance, easy fading, etc. Ease of maintenance and easy process operation
- Summary
- Abstract
- Description
- Claims
- Application Information
AI Technical Summary
Problems solved by technology
Method used
Image
Examples
Embodiment 1
[0019] Aluminum surface pretreatment: conventional aluminum metal surface pretreatment process.
[0020] Oxidation film formation on the surface of aluminum: take the pre-treated clean aluminum piece as the anode, and immerse it in the electrolyte of 170 g / L sulfuric acid solution, and treat it for 60 minutes at a working voltage of 20 volts and an electrolysis temperature of 21 °C to make the aluminum surface get Suitable for compound colored anodized coatings.
[0021] Deposition of metal salts in the pores of the film: Rinse the film-formed aluminum piece with water, then immerse it in a pre-configured 13 g / L stannous sulfate solution, and the electrolytic coloring time is 30 seconds.
[0022] Dye molecules enter the film pores: Rinse the electrolytically colored aluminum piece with water, then immerse it in a pre-configured 0.5 g / L acid dye solution for 3 minutes to obtain a composite colored aluminum piece.
[0023] Sealing treatment: immerse in the blocking solution at ...
Embodiment 2
[0025] Aluminum surface pretreatment: conventional aluminum metal surface pretreatment process.
[0026] Oxidation film formation on the surface of aluminum: take the pre-treated clean aluminum piece as an anode, and immerse it in the electrolyte of 200 g / L sulfuric acid solution, treat it for 30 minutes at a working voltage of 12 volts, and an electrolysis temperature of 18 ° C, so that the aluminum surface can be obtained Suitable for compound colored anodized coatings.
[0027] Deposition of metal salts in film pores: Rinse film-formed aluminum parts with water, then immerse in pre-configured 18 g / L stannous sulfate solution, electrolytic coloring time is 3 minutes.
[0028] Dye molecules enter the membrane pores: Rinse the electrolytically colored aluminum piece with water, then immerse it in a pre-configured 3 g / L direct dye solution for 15 minutes to obtain a composite colored aluminum piece.
[0029] Sealing treatment: immerse in the blocking solution at a temperature ...
Embodiment 3
[0031] Aluminum surface pretreatment: conventional aluminum metal surface pretreatment process.
[0032] Oxidation film formation on the surface of aluminum: take the pre-treated clean aluminum piece as the anode, and immerse it in the electrolyte of 180 g / L sulfuric acid solution, and treat it for 40 minutes at a working voltage of 18 volts and an electrolysis temperature of 20 ° C to make the aluminum surface get Anodized film suitable for composite coloring
[0033] Deposition of metal salts in film pores: Rinse film-formed aluminum parts with water, then immerse in pre-configured 14 g / L stannous sulfate solution, electrolytic coloring time is 60 seconds.
[0034] Dye molecules enter the membrane pores: Rinse the electrolytically colored aluminum piece with water, then immerse it in a pre-configured 1.5 g / L acid dye solution for 8 minutes to obtain a composite colored aluminum piece.
[0035] Sealing treatment: immerse in the blocking solution at a temperature of 60-65°C f...
PUM
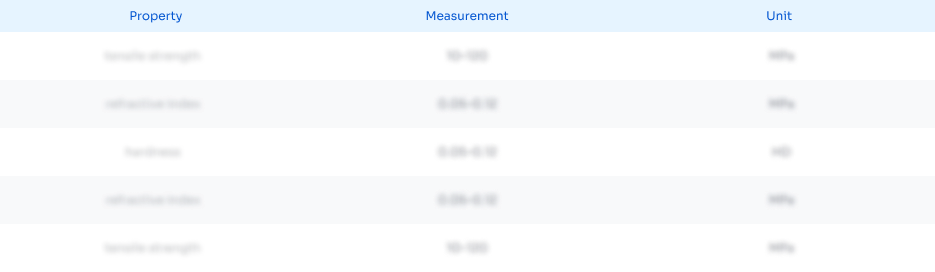
Abstract
Description
Claims
Application Information

- Generate Ideas
- Intellectual Property
- Life Sciences
- Materials
- Tech Scout
- Unparalleled Data Quality
- Higher Quality Content
- 60% Fewer Hallucinations
Browse by: Latest US Patents, China's latest patents, Technical Efficacy Thesaurus, Application Domain, Technology Topic, Popular Technical Reports.
© 2025 PatSnap. All rights reserved.Legal|Privacy policy|Modern Slavery Act Transparency Statement|Sitemap|About US| Contact US: help@patsnap.com