Method of preparing glass fibre needled felt reinforced thermoplastic composite material
A technology for reinforcing thermoplastics and glass fibers, applied in chemical instruments and methods, lamination devices, lamination auxiliary operations, etc., can solve the problems of easy decomposition of resin, high viscosity of thermoplastic melt, difficulty of impregnating fibers, etc., and achieve less environmental pollution , The effect of good mechanical properties of materials and low cost of material preparation
- Summary
- Abstract
- Description
- Claims
- Application Information
AI Technical Summary
Problems solved by technology
Method used
Examples
Embodiment 1
[0015] Prepare water suspension according to the ratio of PVC paste resin to water 5:14, then add ACR-401 accounting for 1% of the mass of PVC paste resin and methyl mercaptide stabilizer accounting for 3% of the mass of PVC paste resin and mix evenly to make water Suspension, impregnating a single-layer continuous glass fiber mat with a glass fiber content of 30% in water suspension, passing through a drying tunnel to remove water, and then hot pressing with double steel belts to make a prepreg tape;
[0016] Cut the prepreg tape into the size and shape of the mold, take three layers and put them into the mold, preheat for 10 minutes, heat press on a flat vulcanizing machine for 25 minutes at a temperature of 190°C and a pressure of 10Mpa to make a PVC / GMT sheet, and demould Obtain the composite material. Finally, the plate is made into a spline according to the standard. The test results are shown in Table 1:
[0017] mechanical properties
Embodiment 2
[0019] Prepare water suspension according to the ratio of PVC paste resin to water 5:10, then add ACR-401 accounting for 4% of the mass of PVC paste resin and tin methyl mercaptide stabilizer accounting for 6% of the mass of PVC paste resin and mix evenly to make water Suspension, impregnating a single-layer continuous glass fiber mat with a glass fiber content of 35% into the water suspension, passing through a drying tunnel to remove water, and then hot-pressing with double steel belts to make a prepreg tape;
[0020] Cut the prepreg tape into the size and shape of the mold, take three layers and put them into the mold, preheat for 10 minutes, heat press on a flat vulcanizing machine for 25 minutes at a temperature of 200°C and a pressure of 10Mpa to make a PVC / GMT sheet, and demould Obtain the composite material.
[0021] Finally, the plate is made into a spline according to the standard. The test results are as follows in Table 2:
[0022] mechanical properties ...
Embodiment 3
[0024] Prepare water suspension according to the ratio of PVC paste resin to water 5:22, then add ACR-401 accounting for 2% of the mass of PVC paste resin and methyl mercaptide stabilizer accounting for 4% of the mass of PVC paste resin, and mix evenly to prepare Water suspension, impregnating a single-layer continuous glass fiber mat with a glass fiber content of 33% into the water suspension, passing through a drying tunnel to remove water, and then hot-pressing with double steel belts to make a prepreg tape;
[0025] Cut the prepreg tape into the size and shape of the mold, put three layers into the mold, preheat for 10 minutes, mold at a temperature of 195°C and a pressure of 10Mpa for 25 minutes, and demould to obtain the composite material.
[0026] Finally, the plate is made into a spline according to the standard. The test results are shown in Table 3 below:
[0027] mechanical properties
PUM
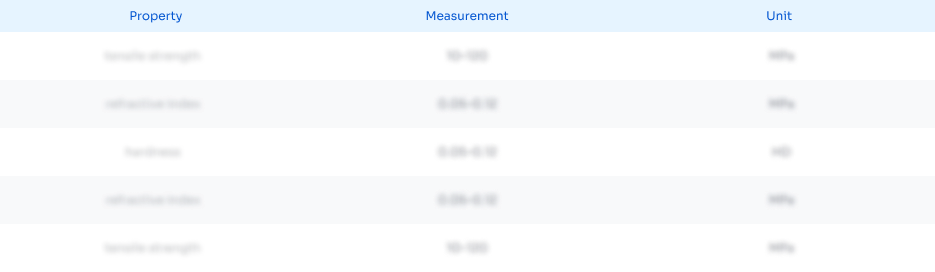
Abstract
Description
Claims
Application Information

- R&D Engineer
- R&D Manager
- IP Professional
- Industry Leading Data Capabilities
- Powerful AI technology
- Patent DNA Extraction
Browse by: Latest US Patents, China's latest patents, Technical Efficacy Thesaurus, Application Domain, Technology Topic, Popular Technical Reports.
© 2024 PatSnap. All rights reserved.Legal|Privacy policy|Modern Slavery Act Transparency Statement|Sitemap|About US| Contact US: help@patsnap.com