Wear resistant type plastic floor and its production technology
A plastic floor, wear-resistant technology, used in the field of decoration materials, can solve the problems of short service life, low mechanical properties, water resistance, poor wear resistance, etc., and achieve excellent mechanical properties, weather resistance and corrosion resistance.
- Summary
- Abstract
- Description
- Claims
- Application Information
AI Technical Summary
Problems solved by technology
Method used
Image
Examples
Embodiment 1
[0038] Embodiment 1: The production process steps of the wear-resistant plastic floor in the embodiment of the present invention are as follows:
[0039] 1. Mixed and extruded plastic foam floor substrate main and auxiliary materials:
[0040] Firstly, waste plastics (extruded thermosetting plastics PE or PP or PET): such as plastic bottles, plastic basins, etc. are crushed and ground into waste plastic powder with a fineness of 200 meshes, and then spontaneously ignited and dried for use.
[0041] Get waste plastic powder: 35% by weight, add active calcium carbonate (stone powder) to: 55% by weight, plastic reinforcing agent selects chlorinated polyethylene (CPE) as: 2% by weight, plastic filler selects calcium carbonate (stone powder) as: : 3% by weight, calcium stearate is selected as the plastic processing aid: 5% by weight, through high-speed mixing, mixing temperature: 100 ℃, mixing time, 10 minutes, rotating speed: 100 rev / min; Form plastic foam pellets, the temperatur...
Embodiment 2
[0048] 1. Mixed and extruded plastic foam floor substrate main and auxiliary materials:
[0049] Firstly, waste plastics (extruded thermosetting plastics PE or PP or PET) are crushed and ground into waste plastic powder with a fineness of 200 meshes, and then dried naturally for use.
[0050]Get PVC resin powder in the embodiment of the present invention: 45% by weight, add active calcium carbonate (stone powder) to: 45% by weight, plastic reinforcing agent selects methyl methacrylate copolymer as: 3% by weight, plastic filler selects carbonic acid for use Calcium (stone powder) is: 2% by weight, and the plastic processing rib agent is selected from AC foaming agent Azodicarbonamide (DN12) is: 5% by weight, mixed at a high speed, mixing temperature: 110 ° C, mixing time, 13 minutes, Rotational speed: 110 rpm; extruded into plastic foam pellets through extrusion mixer, temperature: 190°C, screw rotational speed: 35 rpm;
[0051] 2. Production of plastic foam floor substrate: ...
Embodiment 3
[0056] 1. Mixed and extruded plastic foam floor substrate main and auxiliary materials:
[0057] Firstly, waste plastics (extruded thermosetting plastics PE or PP or PET) are crushed and ground into waste plastic powder with a fineness of 200 meshes, and then dried naturally for use.
[0058] In the embodiment of the present invention, the PP plastic raw material is: 55% by weight, adding active calcium carbonate (stone powder) is: 35% by weight, the plastic reinforcing agent is chlorinated polyethylene (CPE): 4% by weight, and the plastic filler is selected from sawdust The fiber powder is: 1% by weight, the foaming regulator (ZB530) is selected as the plastic processing aid: 5% by weight, through high-speed mixing, mixing temperature: 120°C, mixing time, 15 minutes, rotating speed: 120 rpm; Extrude the compounder to extrude into plastic foam pellets, the temperature is: 200°C, the screw speed is: 40 rpm;
[0059] 2. Production of plastic foam floor substrate:
[0060] Plas...
PUM
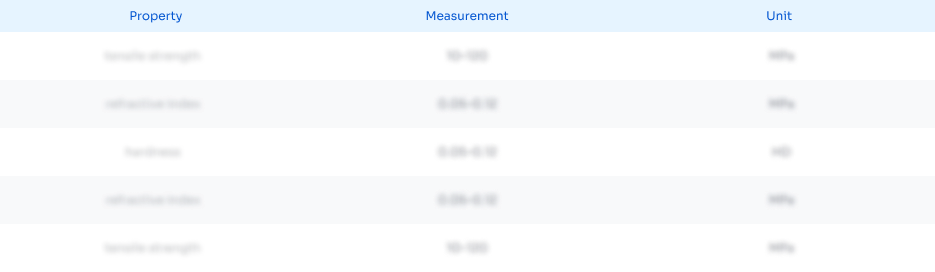
Abstract
Description
Claims
Application Information

- Generate Ideas
- Intellectual Property
- Life Sciences
- Materials
- Tech Scout
- Unparalleled Data Quality
- Higher Quality Content
- 60% Fewer Hallucinations
Browse by: Latest US Patents, China's latest patents, Technical Efficacy Thesaurus, Application Domain, Technology Topic, Popular Technical Reports.
© 2025 PatSnap. All rights reserved.Legal|Privacy policy|Modern Slavery Act Transparency Statement|Sitemap|About US| Contact US: help@patsnap.com