Method for producing J55-grade steel for petroleum casing based on electric furnace sheet billet continuous casting an rolling process
A technology of thin slab continuous casting and petroleum casing, applied in the field of alloy steel production, can solve problems such as no successful experience, achieve the effect of improving the comprehensive performance of steel strip, meeting high strength and high toughness, and improving welding performance
- Summary
- Abstract
- Description
- Claims
- Application Information
AI Technical Summary
Problems solved by technology
Method used
Image
Examples
Embodiment 1
[0037] The electric furnace thin slab continuous casting and rolling process used is: electric furnace smelting, refining, thin slab continuous casting, casting slabs solidified and directly entering the roller hearth heating or soaking furnace, high pressure water descaling, hot rolling, laminar cooling, coiled.
[0038]The chemical composition range of molten steel is: C: 0.16~0.20%, Si: 0.15~0.30%, Mn: 0.85~1.10%, P: 0.01~0.02%, S: 0.003~0.008%, Nb: 0.040%, Ti: 0.022% .
[0039] Thin slab continuous casting and rolling process parameters are: continuous casting casting speed: 3.8-4.6m / min, slab entering furnace temperature: 980-1050°C, soaking temperature: 1160-1200°C, start-rolling temperature: 1080-1120°C , Final rolling temperature: 800-860°C, strong cooling mode, coiling temperature: 550-600°C.
[0040] The organization of the steel belt see figure 1 , the grain size and properties of the strip are shown in Table 1.
[0041] Strip thickness
Embodiment 2
[0043] The electric furnace thin slab continuous casting and rolling process used is: electric furnace smelting, refining, thin slab continuous casting, casting slabs solidified and directly entering the roller hearth heating or soaking furnace, high pressure water descaling, hot rolling, laminar cooling, coiled.
[0044] The chemical composition range of molten steel is: C: 0.16~0.20%, Si: 0.15~0.30%, Mn: 1.0~1.2%, P: 0.01~0.02%, S: 0.005~0.010%, Nb: 0.05%, Ti: 0.033 %.
[0045] Thin slab continuous casting and rolling process parameters are: continuous casting casting speed: 3.8-4.4m / min, slab entering furnace temperature: 980-1050°C, soaking temperature: 1160-1200°C, start-rolling temperature: 1080-1120°C , Final rolling temperature: 830-880°C, coiling temperature: 600-650°C.
[0046] The organization of the steel belt see figure 2 , the grain size and properties of the strip are shown in Table 2.
[0047] Strip thickness
Embodiment 3
[0049] The electric furnace thin slab continuous casting and rolling process used is: electric furnace smelting, refining, thin slab continuous casting, casting slabs solidified and directly entering the roller hearth heating or soaking furnace, high pressure water descaling, hot rolling, laminar cooling, coiled.
[0050] The chemical composition range of molten steel is: C: 0.18-0.22%, Si: 0.25-0.40%, Mn: 0.70-0.90%, P: 0.01-0.02%, S: 0.008-0.015%, Nb: 0.06%, Ti: 0.025% .
[0051] Thin slab continuous casting and rolling process parameters are: continuous casting casting speed: 4.0-4.4m / min, slab entering furnace temperature: 980-1050℃, soaking temperature: 1160-1200℃, start-rolling temperature: 1090-1130℃ , Final rolling temperature: 800-850°C, strong cooling mode, coiling temperature: 550-600°C.
[0052] The organization of the steel belt see image 3 , the grain size and properties of the strip are shown in Table 3.
[0053] Strip thickness
PUM
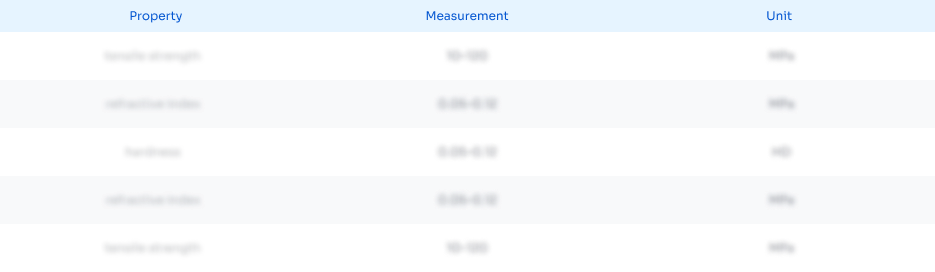
Abstract
Description
Claims
Application Information

- Generate Ideas
- Intellectual Property
- Life Sciences
- Materials
- Tech Scout
- Unparalleled Data Quality
- Higher Quality Content
- 60% Fewer Hallucinations
Browse by: Latest US Patents, China's latest patents, Technical Efficacy Thesaurus, Application Domain, Technology Topic, Popular Technical Reports.
© 2025 PatSnap. All rights reserved.Legal|Privacy policy|Modern Slavery Act Transparency Statement|Sitemap|About US| Contact US: help@patsnap.com