Process for preparing allyl chlorosilane
A technology of allyl chlorosilane and chlorosilane, which can be applied to chemical instruments and methods, compounds of elements of Group 4/14 of the periodic table, and metal/metal oxide/metal hydroxide catalysts, etc. The chlorosilane technology is not too mature, the reaction temperature is high, and the separation of the main product is difficult.
- Summary
- Abstract
- Description
- Claims
- Application Information
AI Technical Summary
Problems solved by technology
Method used
Image
Examples
Embodiment 1
[0024] Place (0.1 mol) rare earth metal samarium in a 100 mL three-necked round bottom flask equipped with a magnetic stirrer, a constant pressure dropping funnel, a reflux condenser, and a gas guide device. Then inject 40 mL of freshly distilled toluene solution, and under the protection of nitrogen, add a slight excess of allyl bromide (0.11 mol) and diphenyldichlorosilane (0.1 mol) to the reaction flask. Stir at room temperature, the solution turns purple-red after 10 minutes, and then react at constant temperature (25°C) for 2 hours. When the solution turns light yellow, stop the reaction. filter. Distill under reduced pressure to obtain colorless allyldiphenylchlorosilane (yield: 98%). Some physical data of the compound are as follows: IR: v max (liquid film)3070.6, 2969.1, 1630.0, 1427.9, 1112.5cm -1 ; 1 H NMR(400MHz, CDCl 3 ): 7.28-7.72 (5H, m, ArH), 5.73-5.83 (1H, m, CH), 5.05-5.09 (2H, t, CH) 2 =), 2.30-2.32(2H, d, CH 2 CH=CH 2 ); 13 C NMR(100MHz, CDCl 3 ): 133.96, 131.77...
Embodiment 2
[0026] Place (0.1 mol) rare earth metal cerium in a 100 mL three-necked round bottom flask equipped with a magnetic stirrer, a constant pressure dropping funnel, a reflux condenser, and an air guide device. Then inject 40 mL of freshly distilled tetrahydrofuran solution, under the protection of nitrogen, add allyl bromide (0.11 mol) and phenyltrichlorosilane (0.05 mol) into the reaction flask. Stir at room temperature, the solution turns purple-red after 10 minutes, and then react at constant temperature (25°C) for 2 hours. When the solution turns light yellow, stop the reaction. filter. Distill under reduced pressure to obtain colorless phenyldiallylchlorosilane (yield: 95%).
Embodiment 3
[0028] Place (0.1 mol) rare earth metal samarium in a 100 mL three-necked round bottom flask equipped with a magnetic stirrer, a constant pressure dropping funnel, a reflux condenser, and a gas guide device. Then inject 40 mL of freshly distilled xylene solution, under the protection of nitrogen, add allyl bromide (0.11 mol) and methyl trichlorosilane (0.1 mol) into the reaction flask. Stir at room temperature, the solution turned purple-red after 10 minutes, and then heated to reflux (110°C) for 12 hours. When the solution turns light yellow, stop the reaction. filter. Distill under reduced pressure to obtain colorless methallyldichlorosilane (yield: 98%).
PUM
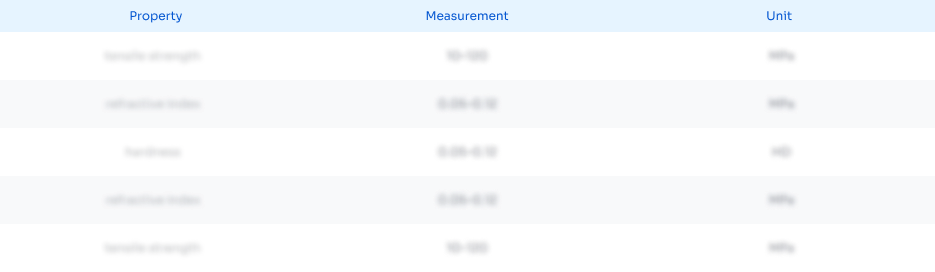
Abstract
Description
Claims
Application Information

- Generate Ideas
- Intellectual Property
- Life Sciences
- Materials
- Tech Scout
- Unparalleled Data Quality
- Higher Quality Content
- 60% Fewer Hallucinations
Browse by: Latest US Patents, China's latest patents, Technical Efficacy Thesaurus, Application Domain, Technology Topic, Popular Technical Reports.
© 2025 PatSnap. All rights reserved.Legal|Privacy policy|Modern Slavery Act Transparency Statement|Sitemap|About US| Contact US: help@patsnap.com