Composition for thermal insulating layer
A technology of composition and thermal insulation layer, applied in the direction of coating, layered products, transportation and packaging, etc., can solve the problems of insufficient insulation, corrosion, loss of insulation, etc.
- Summary
- Abstract
- Description
- Claims
- Application Information
AI Technical Summary
Problems solved by technology
Method used
Examples
preparation example Construction
[0048] (iv) Preparation of the composition
[0049] According to the present invention, the high porosity particles must be added to the resin system and mixed gently under low shear conditions after the other components of the composition have been blended at higher speeds and at moderate to high shear rates. In the most preferred method, the highly porous particles are mixed under very low shear conditions in a separate vessel with a stabilizer (and if necessary, a very small amount of water to form a homogeneous paste). Once a homogeneous paste is obtained, it is added slowly to the blend of the remaining components with stirring, characterized by very low shear.
[0050] In some embodiments of the invention, time can be saved by omitting a separate premix of the high porosity particles and the stabilizer, and slowly adding the high porosity particles to the premix of all other components of the composition, including the stabilizer . This simplification can be used, for ...
Embodiment 1
[0060] (1) Thickener (Rohm & Haas)
[0061] (2) Defoamer (BYK Chemie USA)
[0062] (3) Dispersant (Rohm & Haas)
[0063] (4) Self-crosslinking epoxy acrylic copolymer (MeadWestvaco)
[0064] (5) Neutralizer, co-dispersant (The Dow Chemical Co.)
[0065] (6) EO-PO Copolymer (BASF)
[0066] (7) Silica Airgel (Cabot)
[0067] Components 1 and 2 were mixed in a Cowles mixer for 5 minutes. Components 3, 4 and 5 were then added and mixed for 5 minutes, after which components 6-12 were added with mixing just until a uniform dispersion was obtained. In the final step, the silica airgel particles (component 13) were added slowly and mixed under cover at a low speed not to exceed 500 rpm / hr. A clear liquid coating composition is obtained.
[0068] The insulating properties of coatings prepared from this composition to a thickness of 0.048 inches were measured by ASTM method ASTM C-518. The results shown below demonstrate the coating's outstanding insulating propert...
Embodiment 2
[0074] (1) Defoamer (BYK Chemie USA)
[0075] (2) Dispersant (Rohm & Haas)
[0076] (3) Self-crosslinking epoxy acrylic copolymer (MeadWestvaco)
[0077] (4) Neutralizer, co-dispersant (The Dow Chemical Co.)
[0078] (5) EO-PO Copolymer (BASF)
[0079] (6) Wetting Agents and Defoamers (Air Products and Chemicals)
[0080] (7) Silica Airgel (Cabot)
[0081] Components 1-4 were mixed in a vortex mixer at low speed for 10 minutes. Then component 5 (TiO in the rutile form 2 powder) was slowly transferred to a vortex mixer. The mixture was covered and dispersed on high speed to a Hegman 6 consistency. Reduce mixing speed and add components 6-13 with continued mixing just until a uniform dispersion is obtained. In the final step, the silica airgel particles (component 14) were added slowly and mixed under cover at a low speed not to exceed 500 rpm / hr. A white liquid coating composition is obtained. [Viscosity=3,600-4,400cps(Spindle 3@20rpm)]
[0082] The insul...
PUM
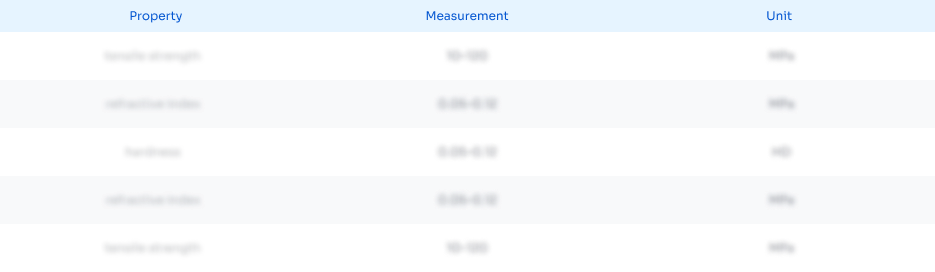
Abstract
Description
Claims
Application Information

- R&D
- Intellectual Property
- Life Sciences
- Materials
- Tech Scout
- Unparalleled Data Quality
- Higher Quality Content
- 60% Fewer Hallucinations
Browse by: Latest US Patents, China's latest patents, Technical Efficacy Thesaurus, Application Domain, Technology Topic, Popular Technical Reports.
© 2025 PatSnap. All rights reserved.Legal|Privacy policy|Modern Slavery Act Transparency Statement|Sitemap|About US| Contact US: help@patsnap.com