Injection moulding method for Ti6A14V alloy gel
A gel injection molding, ti6al4v technology, applied in the field of titanium alloy forming, can solve the problems of component segregation structure, defects and even collapse, unsuitable for large-scale forming, etc., and achieve the effect of low organic content, less body shrinkage, and less organic content.
- Summary
- Abstract
- Description
- Claims
- Application Information
AI Technical Summary
Problems solved by technology
Method used
Image
Examples
Embodiment 1
[0026] The powder is prepared from hydrogenated-dehydrogenated Ti6Al4V powder and gas atomized Ti6Al4V powder, wherein the mass percentage of gas atomized Ti6Al4V powder is 90%. The concentration of acrylamide in the premix is 15%, and the mass ratio of acrylamide:methylenebisacrylamide is 90:1. Add 475 grams of the prepared powder and 1 gram of isooctanol as a defoaming agent to every 100 mL of the premix. After stirring evenly, add catalyst tetramethyl ethylenediammonium (25 μL per 100 mL of slurry), initiator ammonium persulfate (10% by mass, add 15 μL per 100 mL of slurry), stir for 10s, and quickly pour into the mold , drying in an oven at 60°C for 0.5 hours, demoulding, drying in an oven at 60°C for 6 hours, and taking out. in vacuum degree 10 -4 Pa, degreasing at 350°C for 30 minutes, sintering at 1250°C for 3 hours, and cooling with the furnace to obtain titanium alloy parts with better comprehensive mechanical properties and higher dimensional accuracy.
Embodiment 2
[0028] The concentration of hydroxyethyl methacrylate in the premix solution is 20%, and the mass ratio of hydroxyethyl methacrylate:methylenebisacrylamide is 30:1. Add 550 grams of aerosolized Ti6Al4V powder and 2 grams of defoamer fatty acid to each 100mL of the premix. After stirring evenly, add catalyst tetramethylethylenediammonium (30μL per 100mL slurry), initiator potassium persulfate (8% by mass, add 50μL per 100mL slurry), stir for 5s, and quickly pour into the mold , vacuum drying in a 50°C oven for 1 hour, demolding, and drying in an oven at 50°C for 15 hours to take out. in vacuum degree 10 -3 Pa, degreased at 400℃ for 20 minutes, sintered at 1300℃ for 2 hours, and cooled with the furnace to obtain titanium alloy parts with better comprehensive mechanical properties and higher dimensional accuracy.
Embodiment 3
[0030] The powder is prepared from hydrogenated-dehydrogenated Ti6Al4V powder and gas atomized Ti6Al4V powder, wherein the mass percentage of gas atomized Ti6Al4V powder is 80%. The concentration of hydroxypropyl methacrylate in the premix solution is 20%, and the mass ratio of hydroxypropyl methacrylate:methylenebisacrylamide is 100:1. Add 500 grams of prepared powder and 2 grams of defoamer tributyl phosphate to each 100 mL of premix. After stirring evenly, add catalyst tetramethyl ethylenediammonium (30 μL per 100 mL of slurry), initiator ammonium persulfate (10% by mass, add 50 μL per 100 mL of slurry), stir for 5s, and quickly pour into the mold , dried in an oven at 70°C for 0.5 hours, demolded, put in an oven and dried at 70°C for 20 hours and taken out. in vacuum degree 10 -3 Pa, degreasing at 350°C for 30 minutes, sintering at 1300°C for 2 hours, and cooling with the furnace to obtain titanium alloy parts with better comprehensive mechanical properties and higher di...
PUM
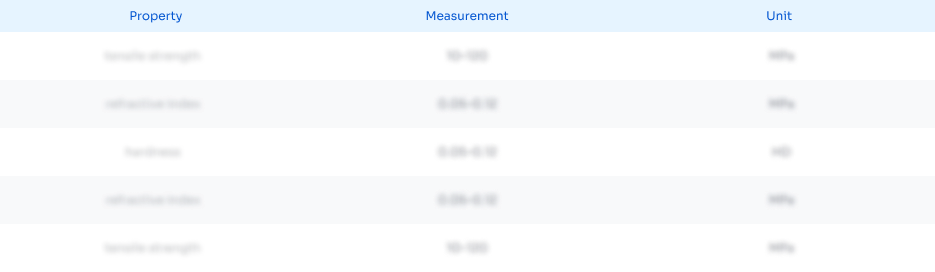
Abstract
Description
Claims
Application Information

- R&D Engineer
- R&D Manager
- IP Professional
- Industry Leading Data Capabilities
- Powerful AI technology
- Patent DNA Extraction
Browse by: Latest US Patents, China's latest patents, Technical Efficacy Thesaurus, Application Domain, Technology Topic, Popular Technical Reports.
© 2024 PatSnap. All rights reserved.Legal|Privacy policy|Modern Slavery Act Transparency Statement|Sitemap|About US| Contact US: help@patsnap.com