Ultra-high coercive force sintered Nd-Fe-B magnetic material and preparing process thereof
A magnetic material, neodymium-iron-boron technology, applied in the direction of magnetic materials, magnetic objects, inorganic materials, etc., can solve the problems of low maximum operating temperature of magnets, high absolute value of temperature coefficient, low intrinsic coercive force Hcj, etc., to achieve The effect of reducing the absolute value of the temperature coefficient, prolonging the life of the equipment, and improving the intrinsic coercive force
- Summary
- Abstract
- Description
- Claims
- Application Information
AI Technical Summary
Problems solved by technology
Method used
Image
Examples
Embodiment 1
[0033] By design composition Nd 25 Dy 4 Tb 4 Fe 59.45 co 6 Nb 0.4 Cu 0.1 Ga 0.05 B 1 (mass fraction, %) Prepare raw materials, smelt into ingots in a medium-frequency vacuum induction melting furnace, break alloy ingots, and grind them into powder by jet milling. The pressure of ~10MPa is compacted and formed, and then isostatic pressed at a pressure of 50~200MPa. The time of isostatic pressing is 5~20 minutes. After isostatic pressing, it is sintered in a vacuum air quenching furnace. 3 hours, the first stage heat treatment temperature is 900°C for 2.5 hours, the second stage heat treatment temperature is 500°C for 2 hours. After being filled with argon and cooled, it was machined into a 10×7 sample, and its magnetic properties were tested (Table 1). Among them, Tw is the highest working temperature of the magnet, Br is 11.2kGs, Hcj is 36kOe, βHcj is -0.40%, (BH)m is 32MGOe.
Embodiment 2
[0040] By design composition Nd 23 Dy 9 Tb 0.5 Fe6 1.1 co 3 Nb 2 Cu 0.1 Ga 0.5 B 0.8 (mass fraction, %) Prepare raw materials, melt them into ingots in a medium-frequency vacuum induction melting furnace, break alloy ingots, and grind them into powder by airflow. The average particle size of the magnetic powder is 4um, and it is oriented in a magnetic field greater than 17KOe. The pressure of 10MPa is compacted, and then isostatic pressing is carried out at a pressure of 50-200MPa. The time of isostatic pressing is 5-20 minutes. After isostatic pressing, it is sintered in a vacuum air quenching furnace. 3 hours, the temperature of the first heat treatment is 900°C, and the time is 3 hours, and the temperature of the second heat treatment is 500°C, and the time is 2 hours. After being filled with argon and cooled, it was machined into a 10×7 sample, and its magnetic properties were tested (Table 2). Where Tw is the maximum working temperature of the magnet.
Embodiment 3
[0047] By design composition Nd 23 Dy 7 Tb 2 Fe 60.32 co 5 Nb 1 Cu 0.5 Ga 0.1 B 1.08 (mass fraction, %) Prepare raw materials, melt them into ingots in a medium-frequency vacuum induction melting furnace, break alloy ingots, and grind them into powder by airflow. The average particle size of the magnetic powder is 4um, and it is oriented in a magnetic field greater than 17KOe. The pressure of 10MPa is compacted, and then isostatic pressing is carried out at a pressure of 50-200MPa. The time of isostatic pressing is 5-20 minutes. After isostatic pressing, it is sintered in a vacuum air quenching furnace. 3 hours, the temperature of the first heat treatment is 900°C, and the time is 3 hours, and the temperature of the second heat treatment is 500°C, and the time is 2 hours. After being filled with argon and cooled, it was machined into a 10×7 sample, and its magnetic properties were tested (Table 3). Where Tw is the maximum working temperature of the magnet.
[0048] ...
PUM
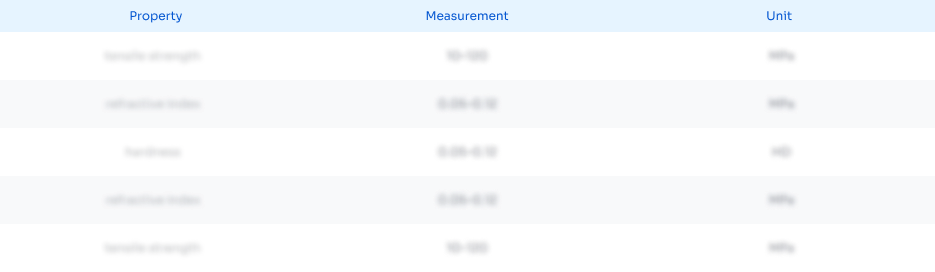
Abstract
Description
Claims
Application Information

- Generate Ideas
- Intellectual Property
- Life Sciences
- Materials
- Tech Scout
- Unparalleled Data Quality
- Higher Quality Content
- 60% Fewer Hallucinations
Browse by: Latest US Patents, China's latest patents, Technical Efficacy Thesaurus, Application Domain, Technology Topic, Popular Technical Reports.
© 2025 PatSnap. All rights reserved.Legal|Privacy policy|Modern Slavery Act Transparency Statement|Sitemap|About US| Contact US: help@patsnap.com