Preparation method of asbestos or non-asbestos rubber latex sheet by paper making process
A latex copy board, non-asbestos technology, used in fiberboard, textiles, papermaking, papermaking, etc., can solve the problems of backward production technology, unfamiliarity, and far distance, and achieve the effect of improving product strength and strength.
- Summary
- Abstract
- Description
- Claims
- Application Information
AI Technical Summary
Problems solved by technology
Method used
Examples
Embodiment 1
[0007] Embodiment 1: first the asbestos fiber is stirred and dispersed so that the mass concentration of the asbestos fiber in water is 1%, after beating, adding calcium carbonate relative to the mass percentage of the asbestos fiber in water and 30% relative to the mass percentage of the asbestos fiber % of carbon black is made into a mixed solution, and the mass percentage concentration of the mixed solution is controlled to be 40%; followed by adding 2% styrene-butadiene latex, 30% sulfur and 0.01% diaryl latex relative to the fiber mass percentage in the mixed solution Mix the secondary amines evenly; finally add 10% silane coupling agent relative to the dry weight of asbestos or non-asbestos fibers in the mixed solution and mix evenly, adjust the pH value of the mixed solution to 7.5 with caustic soda or sodium carbonate , then add sodium fluoride that is 4% relative to the asbestos or non-asbestos fiber quality, mix evenly, pass through the flow delivery system of the pap...
Embodiment 2
[0008] Embodiment 2: First, the asbestos fiber is stirred and dispersed so that the mass concentration of the asbestos fiber in water is 40%, and then adding relative to the asbestos fiber mass percentage is 70% attapulgite powder and relative to the fiber mass percentage is 1% carbon black After beating, the mixed solution is made, and the mass percentage concentration of the mixed solution is controlled to be 20%; followed by adding 25% acrylic latex, 6% morpholine disulfide and 0.2% thiobissulfide relative to the fiber mass percentage in the mixed solution. Substitute phenol and mix evenly; finally add 0.01% silane crosslinking agent relative to the absolute dry weight of asbestos or non-asbestos fibers in the mixed solution and mix evenly, adjust the pH value of the mixed solution to 8.0 with caustic soda or sodium carbonate , and then add 1% sodium fluoride relative to the mass of asbestos or non-asbestos fibers, mix evenly, pass through the flow delivery system of the pap...
Embodiment 3
[0009] Embodiment 3: First, stir and disperse the carbon fiber so that the mass concentration of the carbon fiber in water is 65%, and after beating, add 1% calcium carbonate relative to the carbon fiber mass percentage and 60% carbon black relative to the carbon fiber mass percentage in the water Make a mixed solution, control the mass percent concentration of the mixed solution to be 2.5%; secondly, add 18% nitrile latex, 23% hexamethylenediamine and 8% benzoimidazole to the mixed solution relative to the carbon fiber mass percent and mix evenly Finally, add the titanate coupling agent that is 6% relative to the mass percentage of carbon fiber absolute dry weight in the mixed solution and mix evenly, adjust the pH value of the mixed solution with caustic soda or sodium carbonate to be 8.2, then add relative to asbestos or Sodium fluoride with non-asbestos fiber quality of 0.01% is uniformly mixed and passed through the flow delivery system of the paper machine, and then forme...
PUM
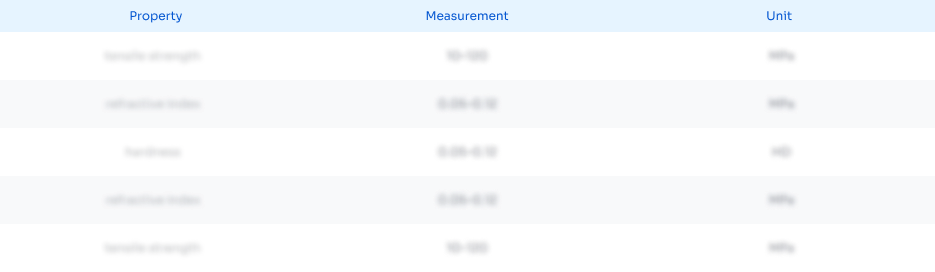
Abstract
Description
Claims
Application Information

- Generate Ideas
- Intellectual Property
- Life Sciences
- Materials
- Tech Scout
- Unparalleled Data Quality
- Higher Quality Content
- 60% Fewer Hallucinations
Browse by: Latest US Patents, China's latest patents, Technical Efficacy Thesaurus, Application Domain, Technology Topic, Popular Technical Reports.
© 2025 PatSnap. All rights reserved.Legal|Privacy policy|Modern Slavery Act Transparency Statement|Sitemap|About US| Contact US: help@patsnap.com