Method for recovering valuable metals from electroplating sludge
A technology of valuable metals and electroplating sludge, which is applied in the direction of improving process efficiency, can solve problems such as poor practicability, large amount of leached slag, and reduced recovery rate, achieving significant economic and social benefits, and easy process conditions The effect of control and easy large-scale production
- Summary
- Abstract
- Description
- Claims
- Application Information
AI Technical Summary
Problems solved by technology
Method used
Examples
Embodiment 1
[0032] (1) 500g of electroplating sludge raw material (Ni6.39%; Cu3.88%; Cr15.7%; Zn2.12%; Fe1.24%; Al5.17%) is first mixed with water and added to 1050ml in dilute sulfuric acid solution, stirred at room temperature for 60 minutes, filtered, and the filtrate was put into the next step for copper precipitation. The filter residue is washed, the washing solution is returned to prepare the leachate, and the washing residue is solidified.
[0033] (2) Add 25 g of sodium sulfide to the 1400 ml filtrate obtained above to react for 1 hour, control the temperature at 90° C., and pH around 1.5, and filter to obtain 30.10 g of copper sulfide and the precipitated mother liquor.
[0034] (3) 15% sodium hydroxide solution is slowly added to the above-mentioned precipitation mother liquor at normal temperature, and the pH value of the control solution is about 5.5, and the precipitation is completed and the mother liquor of 243g of chrome-aluminum slag and iron, zinc and nickel are separat...
Embodiment 2
[0040] (1) Mix 500g of electroplating sludge raw material (Ni4.63%; Cu12.43%; Zn4.23%; Fe17.50%) with water, add it to 1050ml of dilute sulfuric acid solution, and stir at room temperature After 60 minutes, filter, and put the filtrate into the next step for copper precipitation. The filter residue is washed, the washing solution is returned to prepare the leachate, and the washing residue is solidified.
[0041] (2) Add 80 g of sodium sulfide to the 1400 ml filtrate obtained above to react for 1 hour, control the temperature at 90° C., and pH at about 1.5, and filter to obtain 97 g of copper sulfide and precipitated mother liquor.
[0042] (3) Add 63ml of industrial hydrogen peroxide to the above-mentioned mother liquor containing iron, zinc and nickel, use 15% sodium hydroxide solution, adjust the pH at 90°C to about 5.4, keep the temperature for 2 hours, and isolate 143g yellow sodium iron through filtration Alum slag and mother liquor containing zinc and nickel.
[0043]...
Embodiment 3
[0047] (1) 500g of electroplating sludge raw material (Cr8.65%; Zn24.86%; Fe9.92%) is mixed with water first, added in the dilute sulfuric acid solution of 1050ml, stirred at room temperature for 60 minutes, filtered, The filtrate is put into the next step for chromium precipitation. The filter residue is washed, the washing solution is returned to prepare the leachate, and the washing residue is solidified.
[0048] (2) 15% sodium hydroxide solution is slowly added to the above-mentioned precipitation mother liquor at normal temperature, and the pH value of the solution is controlled at about 5.5, and after precipitation is completed, 132g of chrome-aluminum slag and mother liquor containing iron and zinc are separated by filtration.
[0049] (3) Add 44ml of industrial hydrogen peroxide to the above-mentioned mother liquor containing iron and zinc, use 15% sodium hydroxide solution, adjust the pH at 90°C and keep the temperature reaction at about 5.4 for 2 hours, and isolate ...
PUM
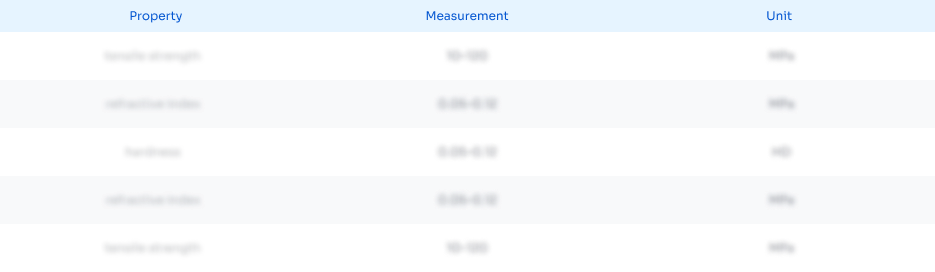
Abstract
Description
Claims
Application Information

- R&D
- Intellectual Property
- Life Sciences
- Materials
- Tech Scout
- Unparalleled Data Quality
- Higher Quality Content
- 60% Fewer Hallucinations
Browse by: Latest US Patents, China's latest patents, Technical Efficacy Thesaurus, Application Domain, Technology Topic, Popular Technical Reports.
© 2025 PatSnap. All rights reserved.Legal|Privacy policy|Modern Slavery Act Transparency Statement|Sitemap|About US| Contact US: help@patsnap.com