Manufacturing technology of hgih pressure bearing glass fiber reinforced plastic oil transfer pipeline
A manufacturing process and oil pipeline technology, which is applied in the field of high-pressure FRP pipeline forming technology, can solve the problems that the external thermal curing system cannot be realized, the curing process temperature cannot be realized, and the heating process cannot be controlled, and the strength performance index can be reliably guaranteed, The effect of small footprint and easy temperature control
- Summary
- Abstract
- Description
- Claims
- Application Information
AI Technical Summary
Problems solved by technology
Method used
Examples
Embodiment Construction
[0010] 1. Wrap the high-pressure glass steel pipe outside the mould: there is a winding trolley on the outside of the mold that can move parallel to the length of the mold. Computer programs are used to control the mold speed and the moving speed of the winding trolley, and the high-strength glass fiber is wound outside the mold for curing. Form a high pressure FRP oil pipeline.
[0011] 2. Curing: Put steam and water into the mold, and use a computer to control the amount of steam circulation and circulating water temperature in the mold. Heat the mold wrapped around the high-pressure FRP oil pipeline at 30°C for 20 minutes, then heat it up to 130°C within 10 minutes, then heat it for 20 minutes, heat it up to 200°C within 10 minutes, and heat it for 20 minutes. Cool down to 80°C inside, keep warm for 20 minutes, then cool down to room temperature. The above-mentioned temperatures are mold cavity temperatures.
[0012] 3. Release the mold after cooling down to room temperat...
PUM
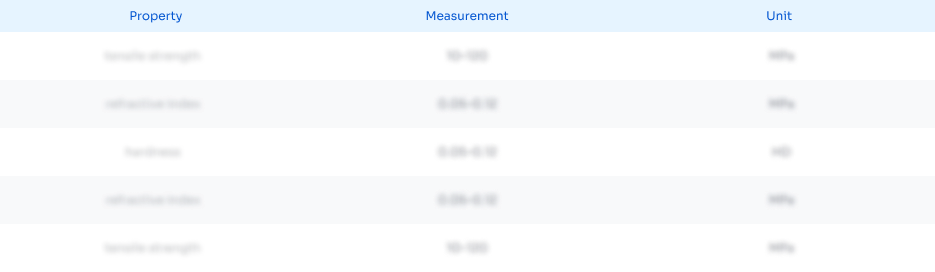
Abstract
Description
Claims
Application Information

- R&D
- Intellectual Property
- Life Sciences
- Materials
- Tech Scout
- Unparalleled Data Quality
- Higher Quality Content
- 60% Fewer Hallucinations
Browse by: Latest US Patents, China's latest patents, Technical Efficacy Thesaurus, Application Domain, Technology Topic, Popular Technical Reports.
© 2025 PatSnap. All rights reserved.Legal|Privacy policy|Modern Slavery Act Transparency Statement|Sitemap|About US| Contact US: help@patsnap.com