Preheat treatment for improving automobile plate of 6111 aluminium alloy formation and baking paint hardening performance
A technology of paint hardening and preheating treatment, applied in the field of alloy heat treatment, to achieve the effects of improving strength, reducing stamping costs, and simple and convenient control
- Summary
- Abstract
- Description
- Claims
- Application Information
AI Technical Summary
Problems solved by technology
Method used
Examples
Embodiment 1
[0011] After the 6111 alloy ingot is homogenized in a circulating air furnace at 470°C×5h+525°C×18h, it is cut and milled, hot-rolled and finally cold-rolled into a thin plate with a thickness of 1.2mm. After the sheet is quenched in a salt bath furnace for solution treatment at 540°C×30min, it is parked at room temperature for 1 day, then heat-treated at 180°C×10min in a drying oven, and stretched and cupped after 2 weeks at room temperature The test, simulating 170℃×30min paint heating treatment is carried out in a drying oven.
Embodiment 2
[0013] After the 6111 alloy ingot is homogenized in a circulating air furnace at 470°C×5h+525°C×18h, it is cut and milled, hot-rolled and finally cold-rolled into a thin plate with a thickness of 1.2mm. After the thin plate is quenched in a salt bath furnace for solution treatment at 540°C×30min, it is parked at room temperature for 2 hours, then heat-treated at 180°C×6min in a drying oven, and stretched and cupped after 2 weeks at room temperature. Burst test, simulating 170 ℃ × 30min baking paint heat treatment is carried out in a drying oven.
Embodiment 3
[0015] After the 6111 alloy ingot is homogenized in a circulating air furnace at 470°C×5h+525°C×18h, it is cut and milled, hot-rolled and finally cold-rolled into a thin plate with a thickness of 1.2mm. After the thin plate is quenched in a salt bath furnace for solution treatment at 540°C×30min, after 5 days at room temperature, it is heat treated at 195°C×8min in an oven, and then stretched and cupped after 2 weeks at room temperature The test, simulating 170℃×30min paint heating treatment is carried out in a drying oven.
PUM
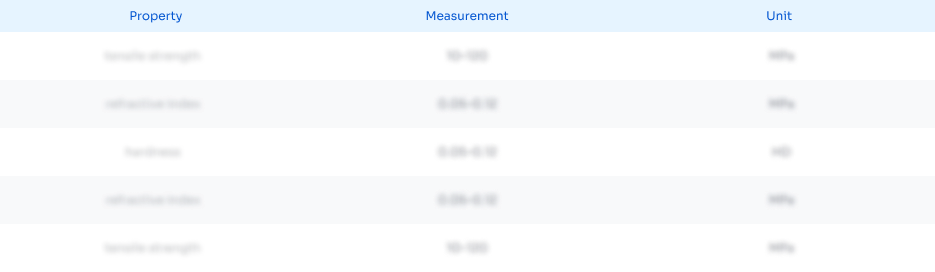
Abstract
Description
Claims
Application Information

- R&D Engineer
- R&D Manager
- IP Professional
- Industry Leading Data Capabilities
- Powerful AI technology
- Patent DNA Extraction
Browse by: Latest US Patents, China's latest patents, Technical Efficacy Thesaurus, Application Domain, Technology Topic, Popular Technical Reports.
© 2024 PatSnap. All rights reserved.Legal|Privacy policy|Modern Slavery Act Transparency Statement|Sitemap|About US| Contact US: help@patsnap.com