Alumina supporter possessing duplicate orifice, catalyst and preparation method
A technology of alumina carrier and double pores, which is applied in the direction of physical/chemical process catalysts, catalyst carriers, chemical instruments and methods, etc., can solve the problems of long process, low yield, easy to overheat, etc., and achieve process simplification and yield High, eliminate the effect of flying temperature
- Summary
- Abstract
- Description
- Claims
- Application Information
AI Technical Summary
Problems solved by technology
Method used
Image
Examples
preparation example Construction
[0022] The preparation method of the catalyst provided by the invention comprises, under the conditions sufficient to deposit molybdenum and / or tungsten and nickel and / or cobalt metal components on the macroporous alumina carrier, combining the macroporous alumina carrier with molybdenum and Solution contacting of / or tungsten and nickel and / or cobalt metal compounds, for example by means of impregnation, co-precipitation, etc., preferably impregnation. Wherein, in terms of oxides, the amount of each component is such that the final catalyst contains 0.5-15% by weight of molybdenum and / or tungsten, and 0.3-8% by weight of cobalt and / or nickel.
[0023] The molybdenum-containing compound is selected from one or more of molybdenum-containing soluble compounds, such as one or more of molybdenum oxide, molybdate, paramolybdate, preferably molybdenum oxide and ammonium molybdate , Ammonium paramolybdate.
[0024] The tungsten-containing compound is selected from one or more of tung...
Embodiment 1
[0032] Take by weighing 300 grams of pseudo-boehmite powder produced by Changling Catalyst Factory, add 10 grams of asparagus powder, 120 grams of ammonium bicarbonate, add an appropriate amount of deionized water after mixing, and knead at room temperature for 15 minutes to become plastic. Extrude into a trilobal strip with a diameter of 1.1 mm on a screw extruder. The wet bar was dried in a drying oven at 120°C for 4 hours, and kept in a roasting furnace at 750°C for 2 hours to obtain carrier A.
Embodiment 2
[0034]Weigh 300 grams of pseudo-boehmite powder produced by Changling Catalyst Factory, add 10 grams of fennel powder, 12 grams of methylcellulose, and 150 grams of ammonium citrate, mix well, add appropriate amount of deionized water, and knead for 10 minutes at room temperature , into a plastic body, extruded into a φ2.5mm cylindrical strip on a screw extruder, and then rolled into a φ2.5mm ball in a spheronizer. The spherical particles were dried at 120°C for 2 hours, and fired in a calcination furnace at 750°C for 2 hours to obtain carrier B.
PUM
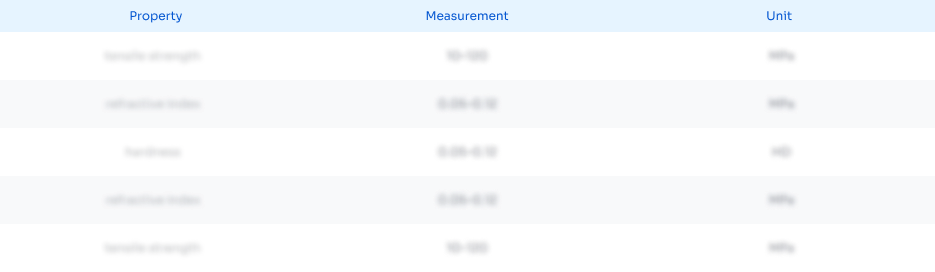
Abstract
Description
Claims
Application Information

- Generate Ideas
- Intellectual Property
- Life Sciences
- Materials
- Tech Scout
- Unparalleled Data Quality
- Higher Quality Content
- 60% Fewer Hallucinations
Browse by: Latest US Patents, China's latest patents, Technical Efficacy Thesaurus, Application Domain, Technology Topic, Popular Technical Reports.
© 2025 PatSnap. All rights reserved.Legal|Privacy policy|Modern Slavery Act Transparency Statement|Sitemap|About US| Contact US: help@patsnap.com