Thermal-shock resistant fireproof brick and production process thereof
A technology for refractory bricks and thermal shock resistance, which is applied in the field of thermal shock-resistant refractory bricks and its production, and can solve the problems of short service life and poor seismic performance of refractory bricks
- Summary
- Abstract
- Description
- Claims
- Application Information
AI Technical Summary
Problems solved by technology
Method used
Examples
Embodiment 1
[0009] The heat-shock resistant refractory brick of the present invention is made of base material and bonding agent, and said base material is by weight: mullite 30%, corundum 35%, α-Al 2 o 3 10% of fine powder, 15% of andalusite and 10% of clay powder. The binder is composed of 30% of 180 mesh andalusite powder, 20% of 180 mesh clay powder and 50% of water. The binder is in the base material The added weight is 10% of the base material weight (ie base material: binder = 100:10 or written as 10:1).
[0010] Such as 1000kg of base material, including 300kg of mullite, 350kg of corundum, α-Al 2 o 3 It is composed of 100kg of fine powder, 150kg of andalusite and 100kg of clay powder. The binder is composed of 30kg of andalusite powder, 20kg of clay powder and 50kg of water. That is, the refractory brick is made of 1000kg of base material and 100kg of binder.
[0011] The production method that realizes embodiment 1 is, at first select base material, by weight: mullite 30% (or...
Embodiment 2
[0013] The heat shock resistant refractory brick of the present invention can also be calculated by weight: mullite 40%, corundum 30%, α-Al 2 o 3 The base material composed of micropowder 8%, andalusite 12% and clay powder 10% is made of a binder composed of 30% andalusite powder, 30% clay powder and 40% water by weight, and the amount of binder added is based on 12% of the weight of the material, such as 10000kg base material is made of mullite 4000kg, corundum 3000kg, α-Al 2 o 3 Micro powder 800kg, andalusite powder 1200kg and clay powder 1000kg, binder is composed of andalusite powder 360kg, clay powder 360kg and water 480kg.
Embodiment 3
[0015] The refractory brick of the present invention can also be made by the following proportions, by weight: 55% mullite, 17% corundum, α-Al 2 o 3 5%, andalusite 15%, clay powder 8% and mud 10% of the total weight of the above materials.
[0016] The process steps to realize embodiment 2 and 3 are the same as embodiment 1, wherein the refractory brick molding process (method) can also adopt the refractory brick molding method of patent application number 200510107273.7, and will not be repeated.
[0017] It can be seen from the above that the composition of the refractory brick of the present invention is completely different from that of the existing anti-shock refractory bricks, and the binder is not made of existing lignin or simple water, and is fired at a high temperature above 1450°C. It is scientific and reasonable. After testing, the load softening start temperature of the heat shock resistant refractory brick made by the present invention is above 1500°C. The ther...
PUM
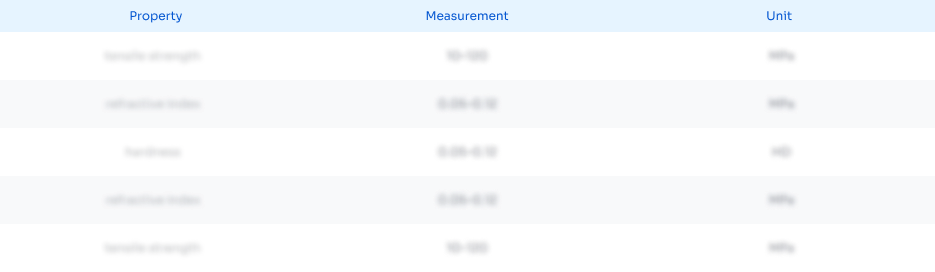
Abstract
Description
Claims
Application Information

- R&D
- Intellectual Property
- Life Sciences
- Materials
- Tech Scout
- Unparalleled Data Quality
- Higher Quality Content
- 60% Fewer Hallucinations
Browse by: Latest US Patents, China's latest patents, Technical Efficacy Thesaurus, Application Domain, Technology Topic, Popular Technical Reports.
© 2025 PatSnap. All rights reserved.Legal|Privacy policy|Modern Slavery Act Transparency Statement|Sitemap|About US| Contact US: help@patsnap.com