Method for manufacturing optical fiber array connector
A manufacturing method and connector technology, applied in the field of optical communication, can solve the problems of cumbersome procedures, connector expansion, low production efficiency, etc., and achieve the effect of simple process
- Summary
- Abstract
- Description
- Claims
- Application Information
AI Technical Summary
Problems solved by technology
Method used
Image
Examples
Embodiment 1
[0033] Focus a 5mW femtosecond laser with a pulse frequency of 10Hz and a wavelength of 800nm on the bottom of a 5mm thick polished quartz glass with a 100x lens, and then scan from bottom to top at a speed of 5μm / s to form 2 laser beams with an interval of 250μm. × 2 wires. Then soak in 4wt% hydrofluoric acid solution, and apply ultrasonic waves, forming a through-hole array with a diameter of 125 μm and a trumpet structure on the surface. And the accuracy of the distance between the through holes is 250±1 μm. Insert the optical fiber into the hole and fix it with an adhesive to form an optical fiber array connector for optical communication.
Embodiment 2
[0035] Focus the 100mW femtosecond laser with pulse frequency of 1KHz and wavelength of 750nm on the bottom of the 5mm thick polished quartz glass with a 50 times lens, and then scan from bottom to top at a speed of 1000μm / s to form 6 laser beams with an interval of 250μm. ×6 wires. Then soak in 4wt% hydrofluoric acid solution, and apply ultrasonic waves, forming a through-hole array with a diameter of 125 μm and a trumpet structure on the surface. And the accuracy of the distance between the through holes is 250±1 μm. Insert the optical fiber into the hole and fix it with an adhesive to form an optical fiber array connector for optical communication.
Embodiment 3
[0037] Focus the 500mW femtosecond laser with pulse frequency of 200KHz and wavelength of 850nm on the bottom of 5mm thick polished quartz glass with a 2x lens, and then scan from bottom to top at a speed of 5000μm / s to form 10 laser beams with an interval of 250μm. ×10 wires. Then soak in 4wt% hydrofluoric acid solution, and apply ultrasonic waves, forming a through-hole array with a diameter of 125 μm and a trumpet structure on the surface. And the accuracy of the distance between the through holes is 250±1 μm. Insert the optical fiber into the hole and fix it with an adhesive to form an optical fiber array connector for optical communication.
PUM
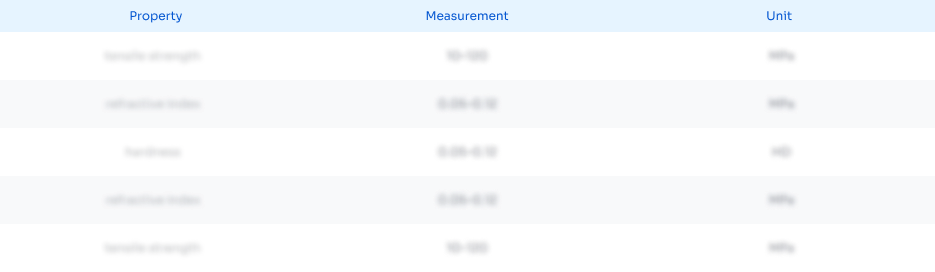
Abstract
Description
Claims
Application Information

- Generate Ideas
- Intellectual Property
- Life Sciences
- Materials
- Tech Scout
- Unparalleled Data Quality
- Higher Quality Content
- 60% Fewer Hallucinations
Browse by: Latest US Patents, China's latest patents, Technical Efficacy Thesaurus, Application Domain, Technology Topic, Popular Technical Reports.
© 2025 PatSnap. All rights reserved.Legal|Privacy policy|Modern Slavery Act Transparency Statement|Sitemap|About US| Contact US: help@patsnap.com